8 декабря в Москве прошла третья конференция «Информационные технологии в металлургии – 2021». Металлургическая отрасль сегодня продолжает удерживать передовые позиции по уровню интенсивности запуска новых проектов цифровой трансформации в нашей стране. Основной целью форума является формирование конструктивной,
Особенности цифровых двойников в металлургии
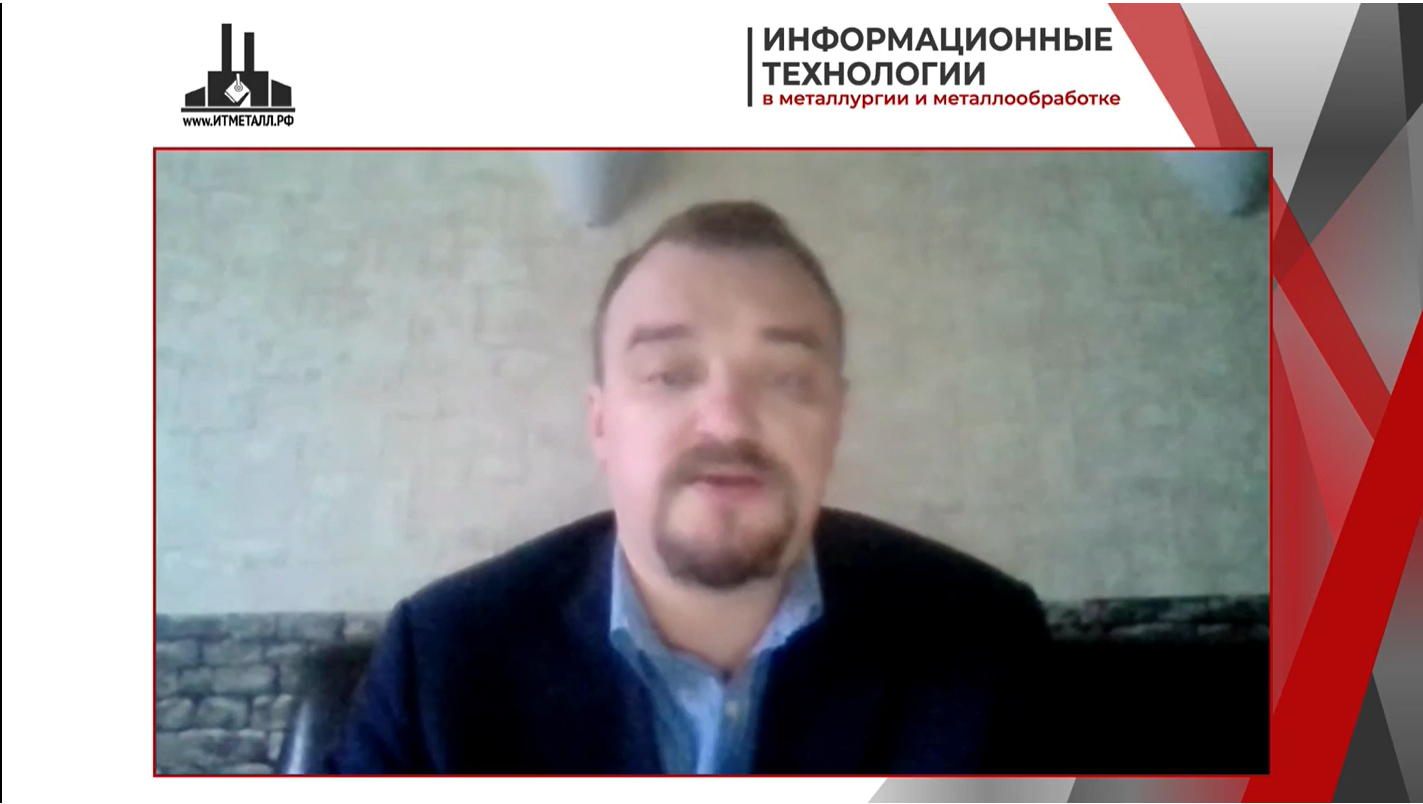
Третья конференция открылась панельной дискуссией по теме «Цифровые двойники в металлургии: сегодня и завтра», обязанности модератора которой взял на себя Дмитрий Корешков, заместитель генерального директора ИД «Коннект». В панельной дискуссии приняли участие:
- Иван Герасимов, заместитель директора по производству (по совершенствованию производственных потоков), АО «Чепецкий механический завод»;
- Всеволод Глущенко, эксперт по развитию новых технологий ОАО «Северсталь-Инфоком»;
- Артем Губайдуллин, заместитель руководителя по реализации проектов в области Индустрии 4.0 ОАО «ММК-МЕТИЗ»;
- Александр Севостьянов, начальник Управления информационной безопасности СЭБ ПАО «ТМК»;
- Андрей Федотов, ведущий эксперт по автоматизации и цифровым технологиям ПАО «Северсталь»;
- Евгений Шкуратов, начальник отдела цифровизации и технологий ООО «ТМК НТЦ».
Модератор дискуссии предложил начать обсуждение с общих вопросов: с понимания предмета обсуждения, особенностей технологии цифрового двойника в металлургии и металлообработке, специфики отрасли, состава цифрового двойника применительно к изделию и производству в целом, предполагаемой и действительной функциональности двойника, принципов управления и оптимизации физического объекта или процесса.
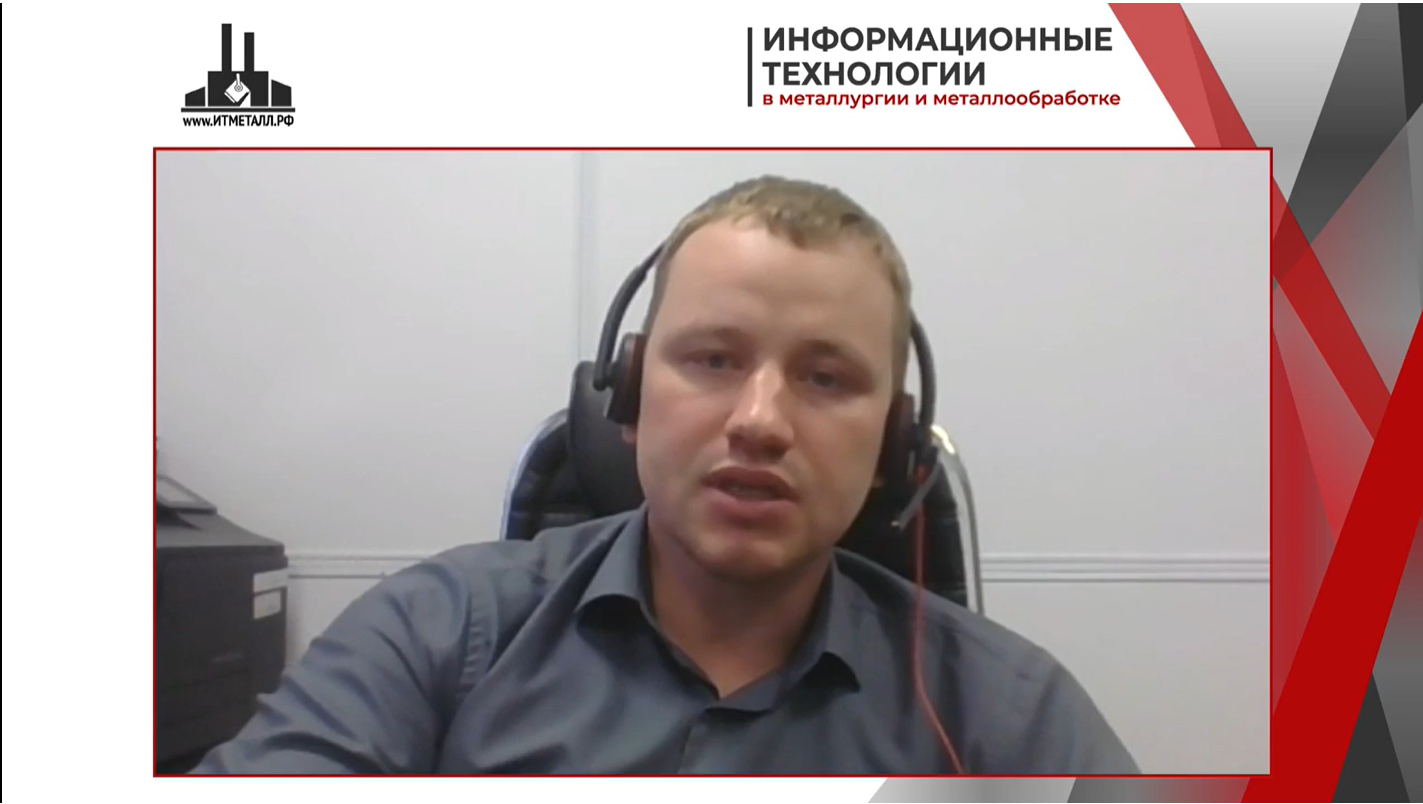
«Цифровой двойник – это, прежде всего, программное обеспечение, которое реализует определенную функциональность», – считает Андрей Федотов. Что отличает цифровой двойник от других моделей? 1) Данное ПО непрерывно отображает свойства какого-то реального объекта. Какой-то физический объект – единицу продукции, агрегат, линию – мы переносим в цифровой мир и отображаем те свойства, которые нас прежде всего интересуют в данном объекте, с точки зрения решаемой задачи. 2) С помощью цифрового двойника мы можем проигрывать определенные сценарии, меняя какие-то параметры этой модели, чтобы анализировать изменения объекта, в зависимости от заданных условий. По факту, с этой целью и создается цифровой двойник: чтобы быстро, дешево и безопасно проверить, как изменения скажутся на реальном объекте, при этом, не затрагивая этот самый реальный объект. «Например, вам необходимо основательно поменять технологию прокатки стана, понятно, что экспериментировать на живом объекте, перебирая сотни его параметров – слишком дорогостоящее удовольствие. Есть большие риски, что ы конечном итоге вы произведете некачественный продукт, получите аварийные простои и т.д. Ясно, что подобные эксперименты разумнее ставить в безопасной цифровой среде, на цифровом двойнике», – пояснил свою мысль Андрей Федотов. 3) Модель объекта должна приносить какой-то положительный эффект – она встраивается в бизнес-процесс, чтобы вы могли выстроить вокруг нее систему управления. Прежде чем приступать к созданию цифровой модели, необходимо четко ответить себе на вопрос: а зачем мы это делаем? Ответив на этот ключевой вопрос, вы далее сможете ответить и на другие вопросы, какой именно цифровой двойник вам нужен (с каким уровнем абстракции), как именно он должен работать, как вы сможете использовать его на производстве?
«Металлургия – это не самая гибкая отрасль, с точки зрения возможности изменения основных бизнес-процессов. Кроме того, крупные металлургические компании сейчас обрастают MES- и ERP-системами, что также сдерживает быстроту изменений. Мы не можем быстро разработать масштабный цифровой двойник и полностью перестроить бизнес вокруг цифровой модели – потребуется очень много изменений, валидаций и пр. Поэтому на данный момент мы больше применяем цифровые двойники для имитации работы лишь определенных участков, либо отдельных производственных агрегатов. В основном мы применяем цифровые двойники не к изделию, а к процессу», – отметил Андрей Федотов.
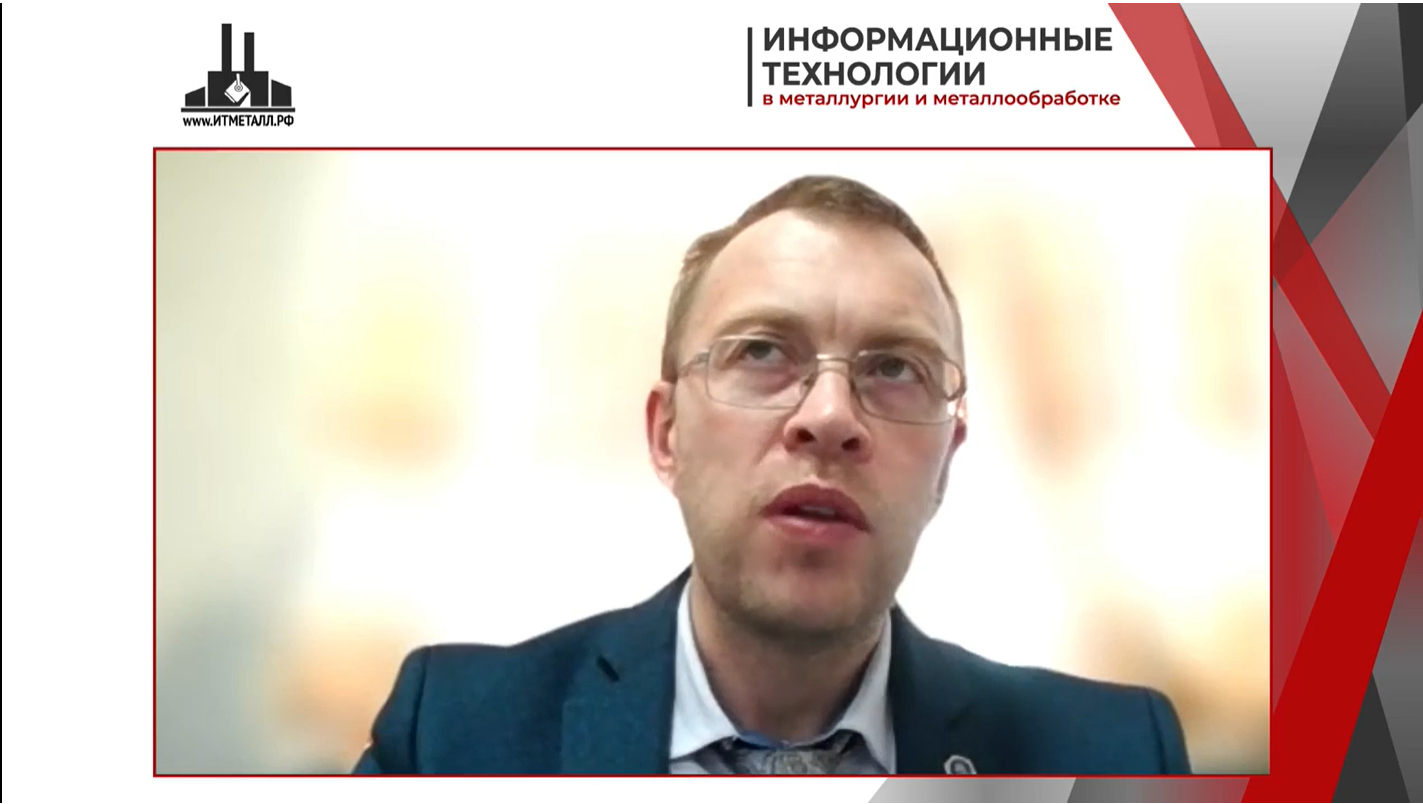
«В нашем понимании цифровой двойник – это некая информационная система, которая содержит набор параметров реально действующего оборудования», – заявил Артем Губайдуллин. – «Например, цифровым двойником является информационная модель стана, отображающая его характеристики в режиме реального времени. Она позволяет производить диагностику на лету – мы видим, в каком режиме работает тот или иной механический узел стана, как происходит подготовка и изготовление продукции. На основании получаемых данных мы можем делать предиктивные выводы о качестве изготавливаемой продукции. В базах данных накапливаются сведения о реальном состоянии агрегата, на основании которых можно предсказывать продолжительность нормальной работы стана, вероятность выхода из строя каких-то его узлов».
Как считает Артем Губайдуллин, к этому же типу решений можно отнести и систему диспетчеризации, которая позволяет в режиме реального времени отслеживать состояние работы стана. Важной частью решения является математический аппарат, который нам и позволяет производить анализ накопленных данных для получения выводов о качестве изготавливаемой продукции.
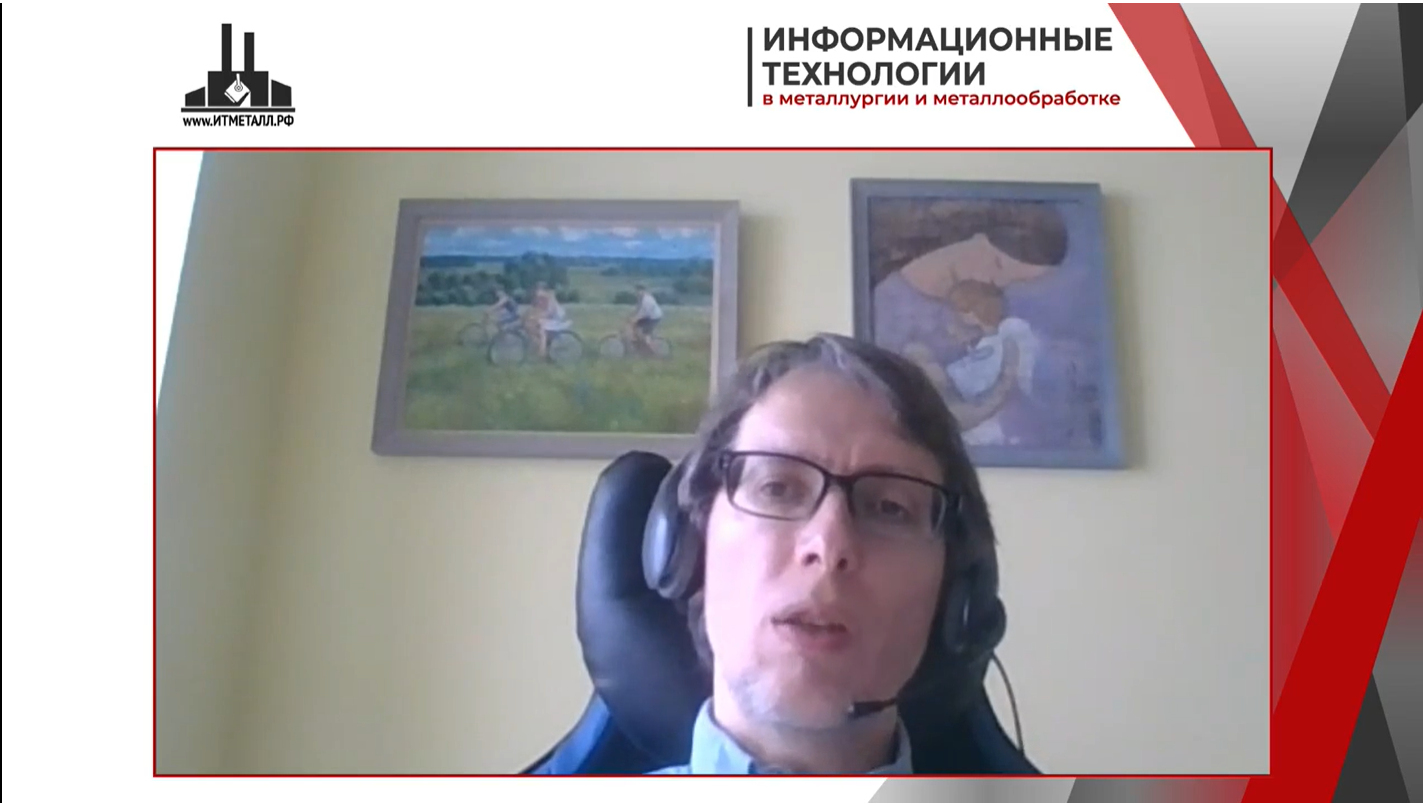
Всеволод Глущенко напомнил участникам дискуссии о том, что приказом Росстандарта утверждены национальные стандарты серии «Численное моделирование» – ГОСТ Р 57700.37-2021 «Компьютерные модели и моделирование. Цифровые двойники изделий. Общие положения». Этот новый стандарт начнет действовать уже с 1 января 2022 года. В ГОСТе было четко сформулировано определение, что цифровой двойник изделия – это система, состоящая из цифровой модели изделия и двусторонних информационных связей с изделием (при наличии изделия) и (или) его составными частями.
«Полноценный цифровой двойник не только воспроизводит некоторые ключевые аспекты процесса или изделия, которые мы хотим моделировать, но и обеспечивает двустороннюю связь с объектом», – подчеркнул Всеволод Глущенко. – «Мы видим в режиме реального времени параметры изделия (оборудования) и можем ими управлять прямо из цифрового двойника. Для всех остальных моделей, которые не располагают подобной двусторонней связью, имеются другие определения – «цифровая тень», «цифровая модель» и т.д. Еще раз: цифровой двойник позволяет нам не только снимать параметры в режиме реального времени, но также управлять оборудованием и моделировать различные ситуации, при этом не останавливая физическое оборудование. Именно это – возможность проигрывать различные ситуации – является ключевым полезным свойством цифровых двойников».
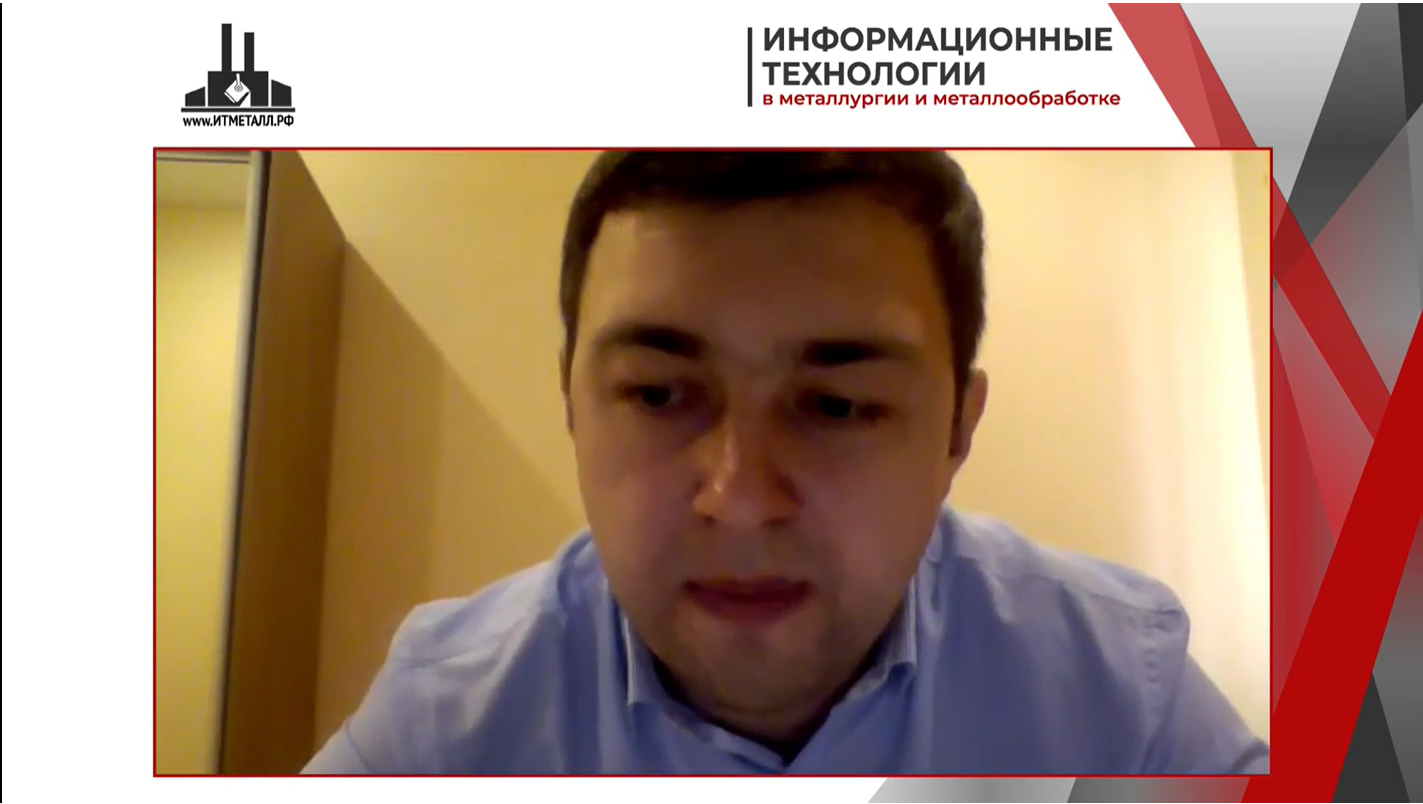
Евгений Шкуратов выразил свою солидарность с предыдущими спикерами, отметив, что цифровой двойник процесса представляет собой программный аналог, моделирующий процессы, технические характеристики и само поведение реального объекта в условиях воздействия различных факторов. При этом Евгений Шкуратов считает необходимым добавить в это определение цифрового двойника рекомендательную систему принятия решений: «Цифровые двойники сегодня – это не просто распиаренный тренд, а вполне состоявшаяся технология, необходимая для производственников».
Говоря о специфике металлургии, Евгений Шкуратов отметил наличие большого набора управляющих параметров: «Если мы будем использовать для моделирования имеющиеся на рынке системы, то очень быстро убедимся в том, что это не эффективно, с точки зрения временных затрат, потому что изменение даже одного параметра отнимает много времени. Поэтому мы разработали свой математический аппарат: комплекс физико-математических моделей по управлению производственным процессом. Изменяя один или целый набор управляющих параметров, мы достигаем необходимой цели в считанные минуты и далее можем рекомендовать те или иные настройки для производственного процесса».
«Цифровой двойник решает две основные задачи – прямую и обратную, – заявил Евгений Шкуратов. – Располагая связью с производством, мы рекомендуем какие-то оптимальные настройки – с точки зрения повышения качества. Но мы можем пойти и от обратного: при получении нового заказа можно задать конечные параметры изделия – цифровой двойник в этом случае может просчитать необходимые параметры технологического процесса».
«Прежде чем подойти к полноценному цифровому двойнику производства, должен быть проделан колоссальный фронт работ: 1) разработан комплекс физико-математических моделей с помощью таких инструментов, как Abaqus, ЛОГОС; 2) произведена адаптация моделей под конкретное производство», – подчеркнул Евгений Шкуратов.
Особенность цифрового двойника, разработанного для «ТМК НТЦ», заключается в том, что он не является неким монолитом, «черным ящиком» – все разбито на микросервисы. Соответственно, в зависимости от решаемой задачи, каждый такой микросервис точно адаптируется под конкретный процесс, оборудование. С точки зрения адаптации и внедрения, такой микросервисный подход дает определенные преимущества.
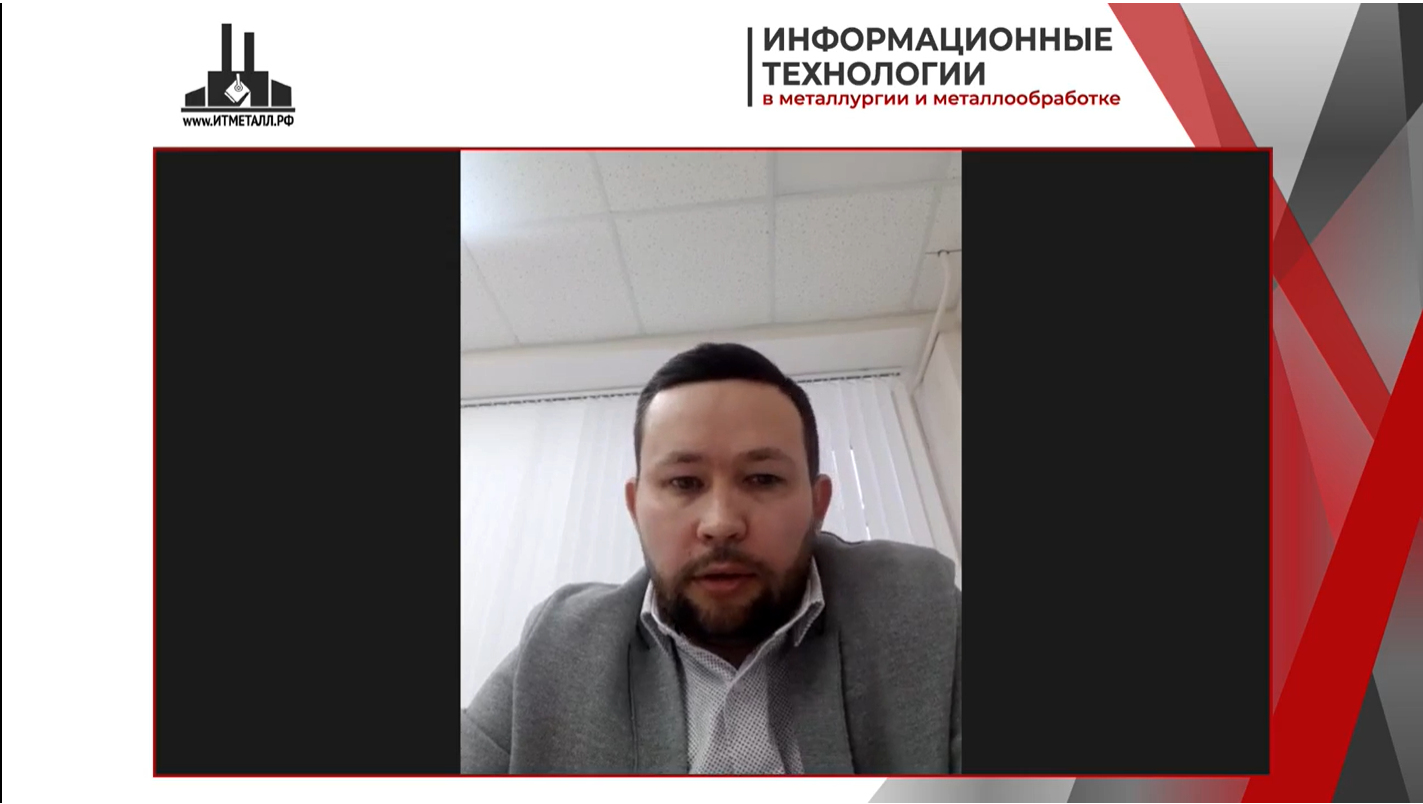
«Объект цифровой модели зависит от поставленной задачи, – читает Иван Герасимов. – Имитационное моделирование, например, позволяет нам сокращать затраты на натурные испытания. Если же говорить о направлении качества, то здесь наибольший интерес будут представлять предиктивная аналитика и контроль параметров по изготовлению изделия. Если посмотреть на производственное направление, то мы будем иметь дело с имитацией процессов планирования изготовления продукции на производственных площадках».
В качестве конкретного примера применения технологии цифровых двойников на производственном направлении Иван Герасимов указал на систему оперативного планирования АО «Чепецкий механический завод»: оперативное перепланирование осуществляется каждые 8 часов, при этом система раскручивает от 10 до 20 тысяч операций в каждом цехе. «Для меня, как для производственника, цифровой двойник – это, в первую очередь, процесс планирования и изготовления продукции на производственной площадке», – пояснил Иван Герасимов.
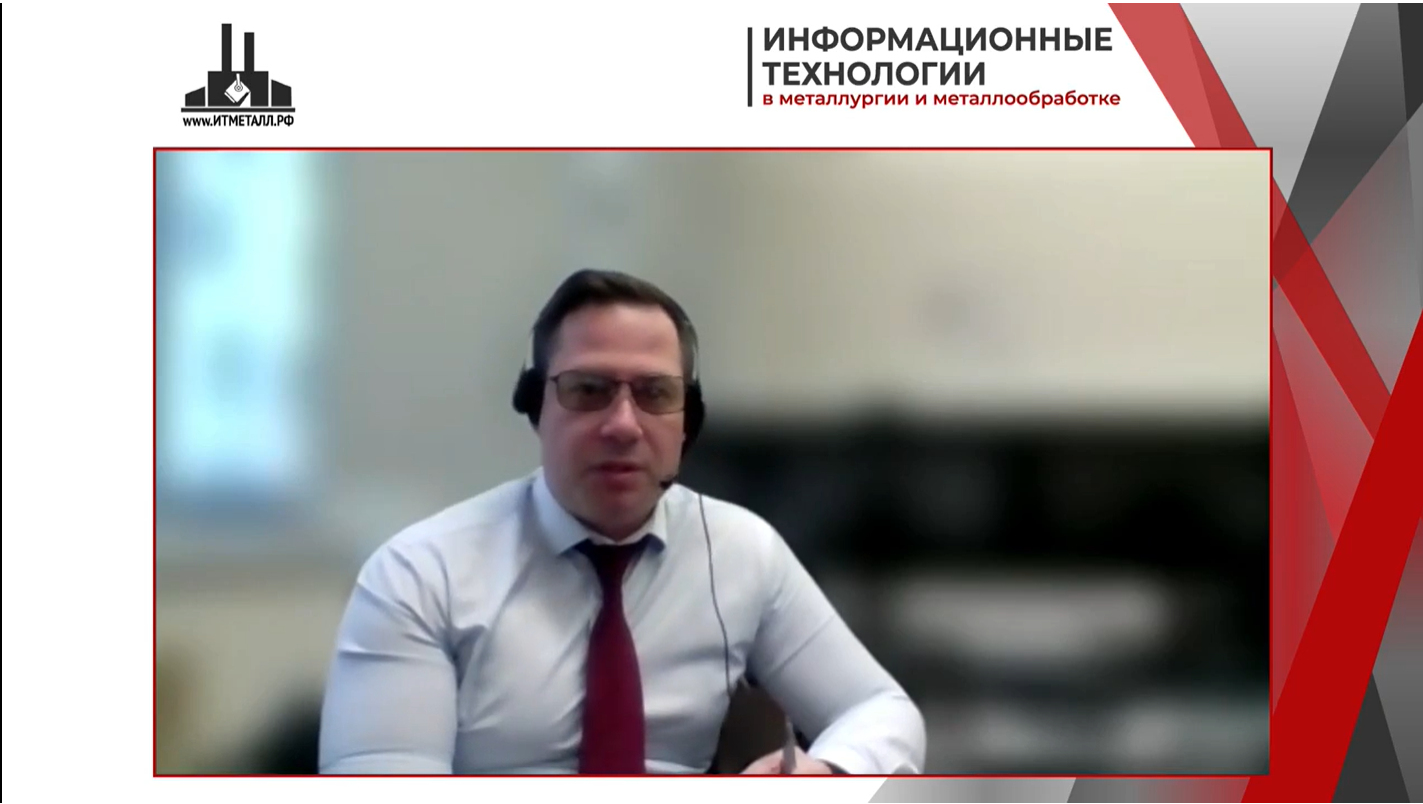
«Поскольку цифровые двойники могут оказывать непосредственное влияние на само производство, из такого прямого управления возникают большие риски, связанные с информационной безопасностью, – считает Александр Севостьянов. – Речь тут идет об объектах критической инфраструктуры. К сожалению, я пока не видел юридических документов, в которых бы говорилось о том, как нам следует поступать с цифровыми двойниками, которые отображают объекты критической инфраструктуры».
Кроме того, возможности прогнозирования, предиктивной аналитики предоставляют определенные конкурентные преимущества. Сам по себе цифровой двойник, как некая модель, обязательно будет объектом пристального внимания со стороны конкурентов, причем, не только российских, но и зарубежных: «Если цифровой двойник способен прогнозировать те или иные процессы производственного предприятия в будущем, то утечка данных из этой системы будет иметь критичный характер».
Таким образом, появление на предприятии цифрового двойника приносит с собой следующие основные риски: 1) риски прямого влияния цифрового двойника на производственный процесс в случае использования системы прямого управления; 2) риски, связанные с промышленным шпионажем, в особенности в том случае, когда цифровой двойник является неким ноу-хау; 3) риски неоправданных капиталовложений, поскольку мы только входим в эпоху «Индустрии 4.0», и пока мало кто понимает, какой конкретный экономический эффект можно получить от этих новых технологий. На какой-то простой поточной линии достаточно легко можно спрогнозировать прибыль, а вот в промышленности, на сложном производстве, так просто это уже не сделать.
Что нам стоит «двойник» построить?
Модератор Дмитрий Корешков предложил участникам обсуждения ответить на вопросы: с чего следует начинать работу с цифровыми двойниками? Какие данные нужны? Какие системы должны быть предварительно развернуты?
Андрей Федотов полагает, что в первую очередь необходимо определиться с бизнес-целью, которую собираетесь решать с помощью цифрового двойника. Впрочем, это правило касается любых цифровых продуктов – не только цифровых двойников. Отсюда вытекает понимание возможных рисков процесса внедрения (потеря инвестиций и пр.) и результатов, которые могут быть достигнуты с помощью новой технологии. Например, если расчеты показывают, что внедрение цифровых двойников позволит вам увеличить объемы производства, и это принесет прибыль в размере нескольких миллиардов, тогда затраты на создание нового ИТ-решения в размере нескольких миллионов, даже при условии высоких рисков, уже не будут казаться такими значительными. Разумеется, поскольку цифровые двойники являются достаточно новым решением, то риски при внедрении этой технологии продолжают оставаться повышенными.
Во-вторых, как считает Андрей Федотов, чтобы приступить к работе с цифровыми двойниками, необходимо понимать, какой процесс, либо какое изделие с помощью цифрового двойника будет оцифрован: «Например, процесс прокатки стали может быть отлично стандартизирован, во многом автоматизирован, на производстве могут быть внедрены сотни датчиков – это значительно упростит процесс оцифровки. Однако может наличествовать и обратная ситуация, например, когда речь идет об агрегате, управление которого полностью завязано на операторе (человеческий фактор) – технологические инструкции для оператора существуют, но в них не определены однозначные параметры производства. По факту, это плохо управляемый процесс, который, как следствие, очень плохо прогнозируем. В этом случае говорить о создании цифрового двойника, наверное, не приходится. Итак, сперва нужно навести порядок в процессах, а уже потом можно их развивать, совершенствовать, получать с них дополнительную выгоду с использованием цифрового двойника. Мы должны перевести производство на иной качественный уровень управления, убрать волатильность процессов до внедрения всяких цифровых технологий, включая цифровых двойников. Иначе все недостатки существующих процессов перетекут в цифровой двойник, который не будет отображать реальность производства. И чтобы качественно управлять процессом, создавать правильны модели, нужны качественные, достоверные данные. Эти данные должны поступать в необходимом объеме, причем, строго в цифровом формате – не в записях журналов от руки. Поэтому, если вы еще не прошли этап сбора данных АСУ ТП в какое-то озеро данных, не прошли этап внедрения MES, не оцифровали ваши процессы с помощью ERP-системы, то рановато говорить о цифровых двойниках».
Всеволод Глущенко поддержал своего коллегу: «Чтобы цифровой двойник состоялся, нам нужно, чтобы базовая автоматизация и инфраструктура передачи данных соответствовали скоростям тех процессов, которые будет охватывать цифровой двойник. Проще говоря, если частота поступления данных недостаточна для отражения в полной мере реальных происходящих процессов, то в этом случае говорить о полноценном цифровом двойнике не приходится, хотя отдельные имитационные модели и позволяют в каких-то аспектах обходится без этого».
Всеволод Глущенко также особо подчеркнул, что понимание того, что производство получит от внедрения цифрового двойника, должно быть четко скоординированным со стороны бизнеса и со стороны ИТ, иначе цифровой двойник не состоится. Он также отметил необходимость существования комплексной инфраструктуры, которая является необходимым пререквизитом появления цифрового двойника: это и цифровые датчики на местах, обеспечивающие наполнение данными цифрового двойника; и инфраструктура, которая позволяет вовремя передавать данные с этих датчиков в озеро; и инфраструктура собственно самого озера данных; и инфраструктура более высокого порядка, стоящая уже над этим озером и осуществляющая далее обработку данных, чтобы цифровой двойник мог исправно функционировать.
Артем Губайдуллин поддержал своих коллег, указав на важность той инфраструктуры, которая позволяет собирать первичные, сырые данные с агрегатов. Соответственно, компании необходима четкая стратегия развития цифровизации и ИТ, инче начинаются сложности: «На производстве зачастую стоят контроллеры от различных производителей – Siemens, Schneider Electric – у них разные протоколы обмена данными, разные форматы самих данных, разное ПО, собирающее данные с агрегатов». Итак, разработка стратегии цифровизации и развития ИТ-инфраструктуры позволит создать общую платформу сбора данных в озеро для их унифицированной обработки.
Евгений Шкуратов отметил, что ТМК в свое время проделал колоссальную работу по апгрейду своего основного оборудования: «Сегодня мы тестируем свои инновационные решения на Северском трубном заводе (СТЗ), поскольку это один из наиболее передовых, высокоавтоматизированных станов российского трубного дивизиона. С точки зрения ИТ-инфраструктуры, сбора данных, работы АСУ ТП – там все построено на высшем уровне: «Внедрение цифровых двойников началось у нас в нужное время, поскольку с момента пуска нового производства было накоплено достаточное количество данных – теперь мы можем проанализировать их и выдать конкретные рекомендации по управлению. Сейчас технологии цифрового двойника помогают нам отыскивать оптимальные решения для того или иного участка на автоматизированном производстве».
Анализируя решения в сфере цифровых двойников, предлагаемые сегодня ведущими вендорами, Андрей Федотов отметил их положительные стороны, но также указан на негативный момент: «Все производители оборудования стремятся подсадить заказчика на свои проприетарные решения. Потом, при попытке интегрировать какое-то ИТ-решение (например, того же цифрового двойника) от другого производителя могут возникнуть очень большие проблемы. Компания должна отдавать приоритет универсальным ИТ-решениям, чтобы оставаться максимально гибкой. К сожалению, все вендоры сегодня запаковывают свои передовые решения в некий «черный ящик», который работает на старте, когда у вас еще действует сервисный контракт на поддержку. А когда возникает потребность что-то изменить в этом «черном ящике», начинаются проблемы, поскольку быстро внести изменения вендор не может. Гораздо удобнее и легче идет дело, когда у заказчика имеются свои компетентные сотрудники, способные оперативно перестраивать достаточно сложные ИТ-решения».
Как отметил Андрей Федотов, чтобы избежать таких рисков попадания в зависимость от вендоров, в ТМК пошли по пути создания собственной ИТ-инфраструктуры, которая не является проприетарным решением от какого-то единственного поставщика, – она была собрана из различных отобранных компонентов и служит универсальной основой для развертывания различных цифровых решения, включая цифровых двойников.
Комментируя высказывания своих коллег о возможностях работы с иностранными вендорами, Александр Севостьянов обратил внимание на существующие санкционные риски. Отвечая на эту реплику, Андрей Федотов ответил: «Мы сегодня с радостью идем в сторону импортозамещения. К сожалению, есть сферы, в которых пока нет российских решений, сопоставимых по качеству с зарубежными разработками. Мы достаточно много используем решения Open Source, покупая у западного вендора только поддержку, либо экспертизу по внедрению».
Всеволод Глущенко отметил, что подход к импортозамещению ПАО «Северсталь» состоит в том, чтобы по максимуму оставить ИТ-решения во внутреннем контуре, по минимуму использовать облака, ни в коем случае не использовать облачные решения для объектов критической инфраструктуры.
Александр Севостьянов подчеркнул, что вопросы, связанные с ИБ, необходимо закладывать в цифровые двойники еще на стадии проектирования ИТ-решения: «Я прекрасно понимаю, что безопасность может входить в некий конфликт с бизнесом – с производственниками и с ИТ-специалистами. Тем не менее, при проектировании таких систем должны обязательно учитываться все законодательные ограничения – другого выхода просто не существует».
Конкретные проекты: проблемы и решения
Модератор озвучил третий блок вопросов, связанных с реализацией конкретных проектов на российских предприятиях, а также предложил участникам рассказать о проблемах и решениях, технической реализации и организации работы, об опыте эксплуатации.
Евгений Шкуратов рассказал о том, как его компания выбирает через акселератор лучшие российские практики, а также ведет и собственные ИТ-разработки, например цифрового двойника процесса прокатки: «Одна из наших новых платформ, которая планируется к внедрению, – это микросервис Roll Position. Чтобы в процессе прокатки стали получить качественную трубу, необходимо постоянно контролировать позиции валков. Сейчас существуют определенные технологические инструкции, действует регламент, который определяет временнóй порядок проверки, но правильнее это делать на основе анализа данных. Так, на основе целостного анализа распределения усиленных гидравлических капсул составляются конкретные рекомендации вальцовщику. Еще один пример: когда мы сформировали нашу ИТ-платформу для моделирования и начали на ней пробовать различные процессы, прогонять сценарии, то заметили, что на непрерывном стане можно использовать оправки меньшей длины, что привело к сокращению закупки материалов».
Как отметил Евгений Шкуратов, в настоящее время на предприятии ведется глобальный проект «цифрового двойника производства», по завершении которого (ориентировочно летом 2022 года) НТЦ получит колоссальный опыт: «Мы объединили в этом проекте несколько отличных подрядчиков, разработчиков, в то время как сами занимаемся вопросами интеграции этой системы».
Артем Губайдуллин рассказал, как на ОАО «ММК-МЕТИЗ» занимаются моделированием текучести металла, а также создают цифровые двойники технологического оборудования: «Обратная связь у нас не реализована по соображениям информационной безопасности – с помощью односторонней системы мы только считываем данные – без возможности какого-либо дальнейшего воздействия на систему со стороны оператора, либо другой информационной системы более высокого уровня. В настоящее время у нас находится в разработке новая цифровая модель индустриального цеха – мы хотим видеть загрузку инструментальных станков для высокоточной обработки металлических заготовок».
«Если вы не готовы отдать вашей модели управление агрегатом или технологическим процессом, то значит вы сами не верите в созданную цифровую модель, – заметил Андрей Федотов. – В таком случае разработанный двойник оказывается хуже текущего процесса, и оператор, стоящий на посту, лучше управляет процессом, чем созданная вами модель».
Рассказывая о передовом опыте, Андрей Федотов указал на создание достаточно точного цифрового двойника агрегата, на котором уже затем был обучен машинный алгоритм обучения с подкреплением. Теперь этот алгоритм по живому, вместо оператора, управляет агрегатом: алгоритм интегрирован с АСУ ТП и работает в защищенном контуре. Почему понадобилось обучать алгоритм на цифровом двойнике? Потому что машинный алгоритм обучения с подкреплением учится методом проб и ошибок, что в принципе невозможно осуществить на реальном агрегате металлургического производства.
Завтрашний день цифровых двойников
В завершение панельной дискуссии модератор предложил участникам порассуждать о перспективах развития, о нормативно-техническом регулировании, доступности платформ и сред для разработки цифровых двойников, подумать об экономическая оправданности и целесообразности цифровых технологий сегодня и завтра.
Артем Губайдуллин считает область цифровых двойников достаточно перспективной, как с точки зрения самих технологий, так и с точки зрения затрат: «Если мы здесь говорим о цифровых двойниках как части имитационного моделирования, то они позволяют нам уже сегодня довольно существенно снижать затраты – мы успешно моделируем физические процессы, избегая затрат на их физическую реализацию».
«ММК-МЕТИЗ» видит хорошие перспективы также и в отношении цифровых двойников технологического оборудования, как в части предиктивной аналитики (своевременного предугадывания выхода из строя какого-либо узла механического оборудования), так и с точки зрения технологии: «Мы можем моделировать производственные процессы, с той или иной степенью вероятности предсказывать выход продукции, как отгружаемой ля потребителя, так и поступающий на какой-то из переделов. Это позволяет нам заметно экономить на возвратах продукции, поскольку существенно снижается риск выхода бракованной продукции».
Артем Губайдуллин отметил, что затраты на цифровые двойники все еще достаточно велики, но в «ММК-МЕТИЗ» считают эти риски оправданными.
Евгений Шкуратов указал на тот факт, что область технологий обработки металлов давлением является достаточно зрелой и консервативной отраслью, и некий прорыв, который обеспечили цифровые двойники, подвиг эту отрасль к совершенствованию: «В молодом поколении я уже сейчас наблюдаю за уклоном в цифру, за непосредственной коллаборацией между технологами и ИТ-специалистами».
Говоря о социальном аспекте, Евгений Шкуратов отметил, что цифровые двойники являются некоей рекомендательной системой, не подменяя собой на 100% человека. Представитель «ММК-МЕТИЗ» считает это положительным фактором, поскольку он снижает степень радикализации производственных реформ.
«В перспективе мы видим развитие микросервисов, компьютерного зрения, предиктивной аналитики, – заявил Евгений Шкуратов. – Еще одной из эффективных и прибыльных тем является предсказание простоев».
Андрей Федотов отметил, что сегодня система управления производством во многом построена на поддержке с помощью расчетов, интуиции и пр., а нам хотелось бы, чтобы управленческие решения принимались с опорой на достаточно точного цифрового двойника производства, позволяющего воспроизводить сценарии того, как решения влияют на компанию в целом, например, спустя один месяц, два месяца и т.д. Такой подход позволил бы избежать множества ошибок и строить бизнес эффективно: «Пока подобного опыта, когда бы вся компания была охвачена цифровым двойником, я не встречал ни в России, ни за рубежом, но к этому надо стремиться».
Ключевые направления цифровизации
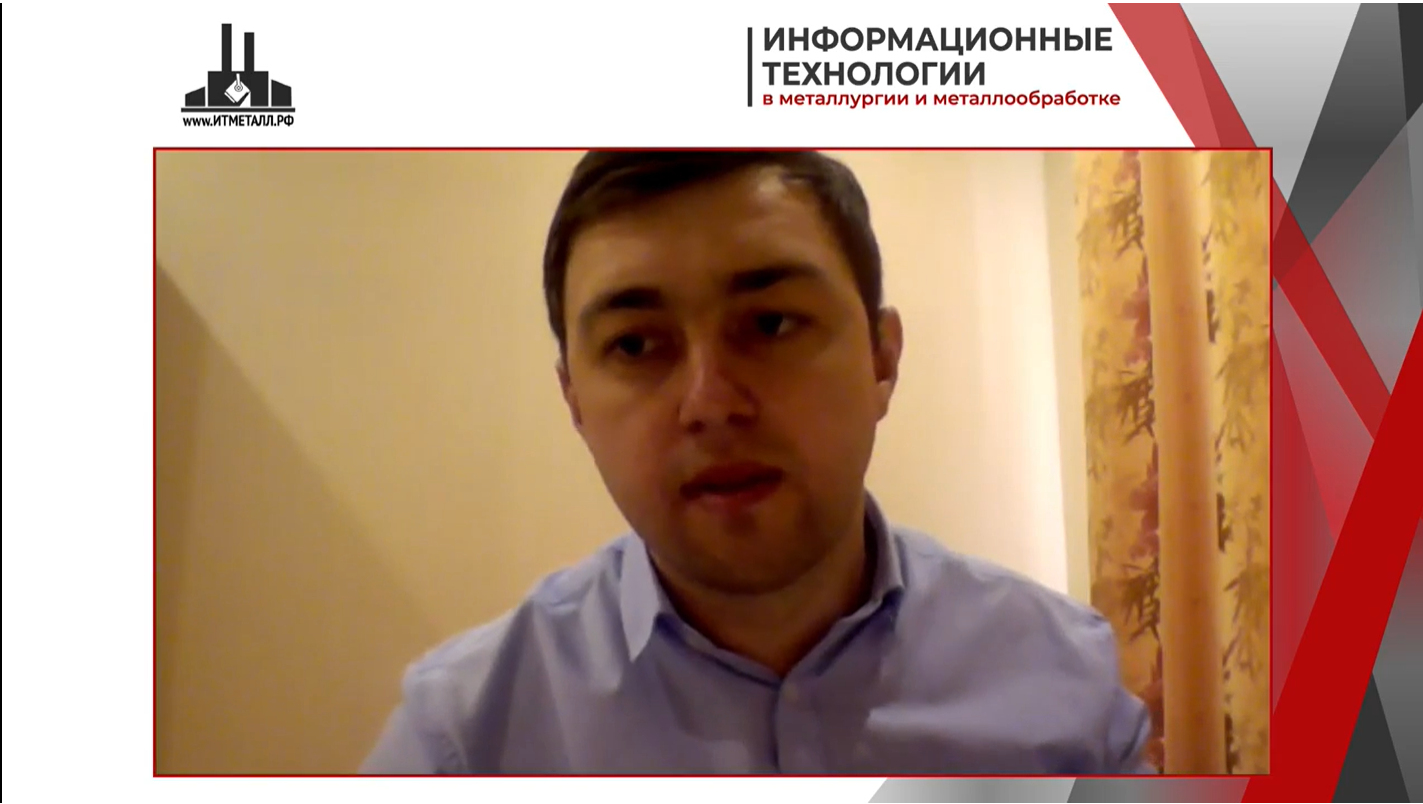
Первую сессию открыл Евгений Шкуратов, начальник отдела цифровизации и технологий ООО «ТМК НТЦ», с докладом на тему «Разработка и внедрение цифровых решений на производственных предприятиях группы ТМК».
ООО «ТМК НТЦ» является центром компетенций по созданию цифровых двойников технологических процессов на основе авторских подходов и комплекса уникальных физико-математических моделей процесса прокатки, специализируется на проведении физических и «цифровых» испытаний. Команда НТЦ – молодые ученые и технологи, лауреаты Премии Правительства РФ по направлению «Цифровой двойник производства».
Основные направления разработки «ТМК НТЦ» – это цифровые двойники, виртуальные ассистенты, системы компьютерного зрения и мобильные приложения. Флагманским направление работ, безусловно, является создание цифровых двойников.
Так, для линий трубопрокатного агрегата ТПЦ «ТАГМЕТ» И ТПЦ-3 «ВТЗ» был создан полноценный программный аналог, моделирующий процессы прокатки труб, технические характеристики, а также поведение реального объекта в условиях воздействий различных факторов. Цифровой двойник аккумулирует опыт эксплуатации стана, теоретические и экспериментальные наработки; позволяет рассчитывать различные деформационные, кинематические и энергосиловые параметры процесса; имеет многопользовательский и многозадачный режим, разграничение прав доступа; построен на основе микросервисной архитектуры. Данный программный продукт учитывает более 5 тысяч настроечных параметров, которые используются при производстве трубной продукции.
«Возможности цифрового двойника позволяют решать не только прямые задачи, но и обратные», – подчеркнул Евгений Шкуратов. – «Одна из основных функций двойника – это обучение: он позволяет персоналу быстро адаптироваться к той или иной работе».
Докладчик также рассказал об интеллектуальных системах управления производством: Roll Positioning, TubeTraceAbility BRCR, TubeLength PIPELINE и TubeCount STC.
Команда «ТМК НТЦ» также занимается созданием мобильных приложений. Например, внедрение системы TubeCounter CV Mobile позволило наладить оперативный контроль количества труб в пакетах различного профиля (круг, квадрат и др.).
Далее, виртуальный ассистент Mill Point Cloud Processing Tool позволяет обеспечивать определение пространственного расположения оборудования непрерывного стана за счет предобработки и анализа данных (облако точек), полученных 3D системой.
Как отметил Евгений Шкуратов, у команды «ТМК НТЦ» уже сформировался пул знаний, наработок и опыта внедрения, что позволило начать проект интеграции сразу 4 продуктов. Целью проекта является переход на новый технологический уровень и создание системы удаленного управления с рекомендательным характером принятия решений. Речь тут идет уже о полноценной системе цифрового двойника производства, а не отдельных объектов.
Результаты внедрения продуктов российских разработчиков: производство продукции высокого качества, внедрение систем неразрушающего контроля на непрерывном производстве; повышение выпуска экспортно-ориентированной продукции; снижение затрат на разработку новых видов продукции; повышение эффективности использования материальных ресурсов и скорости принятия решений за счет использования сквозных цифровых технологий.

Николай Гладких, главный специалист по системам управления качеством ПАО «ММК», выступил с докладом на тему «Качество 4.0 как практическое применение цифровой трансформации в металлургии».
«В эпоху глобальных вызовов и бурного развития ИТ-индустрии мы сейчас, естественно, находимся на этапе пересмотра стратегии развития. Понятно, что и подходы к вопросам качества продукции будут претерпевать большие изменения, если не революционные, то уж точно без эволюционных не обойтись. Все большее влияние на качество в металлургии начинает оказывать так называемая «зеленая сертификация» (углеродный след и т.п.). И наконец, мы видим, что рост влияния потребителей на основе усиления роли открытой информации сейчас получает все больший вес, – отметил Николай Гладких. – Понимая все эти объективные тенденции эпохи, мы стремимся использовать все возможности индустриальной и цифровой революций, чтобы наши клиенты получили реальный результат в виде продукции качественно нового уровня. Поэтому мы свою концепцию качества продукции обозначаем специальным термином – Качество 4.0».
Два года назад в ПАО «ММК» был запущен проект информационной системы «Кнопка» для контроля и повышения технологической дисциплины в цехах сталеплавильного и прокатного производств. Эта система охватывает три уровня производства: I уровень – сталеплавильное производство; II уровень – цеха горячей прокатки; III уровень – цеха холодной прокатки. К настоящему времени удалось привязать всех сотрудников цехов (более 20 тысяч человек) к конкретным агрегатам, которые влияют на выпуск конечной продукции, – вся их работа теперь тщательно документируется. При любом запросе со стороны потребителя можно легко поднять весь массив данных и выяснить, кто и чем именно занимался в такой-то конкретный день.
KPI считается автоматически – любой сотрудник имеет право зайти в кабинет технолога и посмотреть в режиме онлайн, как он действует в течение рабочего дня, месяца, года. На основании обобщенных данных на еженедельной основе ГСУ формирует и направляет в ПСП отчетную информацию по соблюдению технологической дисциплины технологическим персоналом ПСП. Такая система очень помогла вычистить все недостатки, имеющиеся в технологии производства.
Второй вопрос, который должна решать новая система – это привязка претензий к конкретному сотруднику, работавшему над изделием. С этой целью был привязан сводный отчет информационной системы «8D» к системе «Кнопка». «Очень важно, что нам удалось минимизировать человеческий фактор», – подчеркнул Николай Гладких. Была достигнута полная автоматизация сводного отчета по работе ПСП по данным ИС «8D» и ИС «Кнопка». Отчет позволяет по каждой претензии из анализируемого периода сформировать «дерево» плавки. По каждой единице продукции отраженной в дереве плавки существует возможность открыть: паспорт рулона, сквозной паспорт, паспорт нарушений, лабораторные испытания, отгрузочные сертификаты.
Чтобы простимулировать менеджмент и вовлечь руководителей ПСП ПАО «ММК» в процесс управления системой качества, была внедрена система оценки результативности работы руководителей ПСП в части выпуска качественной продукции. Руководители ПСП, получившие желтую и красную оценки работы по качеству за месяц, в течение десяти календарных дней организуют выпуск распоряжения с: 1) определением причин низкой оценки; 2) разработкой конкретных мероприятий, направленных на улучшение контролируемых показателей, назначением ответственных лиц и определением сроков исполнения данных мероприятий.
«За первый же год работы системы некоторые цехи улучшили работу по качеству в 3 раза – не на 3%, а на 300%, – с удовлетворением отметил Николай Гладких. – В XXI веке без цифровизации бизнес-процессов говорить о качестве производства просто невозможно».
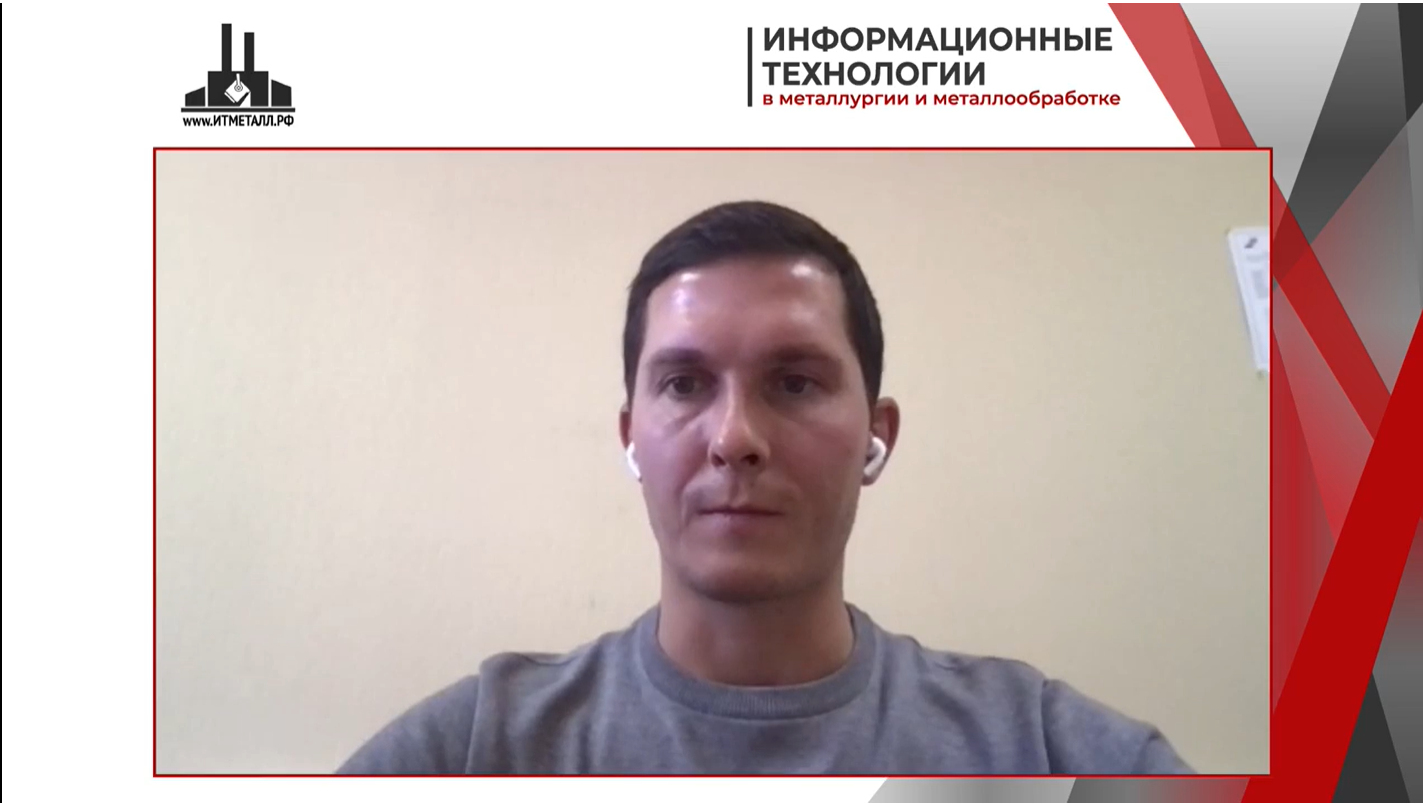
Сергей Борисов-Смирнов, руководитель проекта «Цифровой инжиниринг» АО «ТВЭЛ», рассказал о цифровом инжиниринге в металлургии.
Топливная компания Росатома «ТВЭЛ» сегодня активно развивает новые направления, позволяющее проводить диверсификацию бизнеса: аддитивные технологии, накопители энергии, вывод из эксплуатации, металлургия, специальная химия и оборудование для ТЭК. Одним из перспективных направлений развития бизнеса являются «Цифровые продукты». Портфель услуг цифрового инжиниринга включает в себя: цифровой НИОКР – разработку цифровых двойников новых изделий и продуктовых линеек с помощью цифрового моделирования; цифровые учебные стенды – разработку виртуальных сред обучения для персонала, взаимодействующего со сложными, опасными технологическими объектами; цифровую модернизацию предприятия – исследование производственной площадки для нахождения оптимального пути модернизации.
Цифровой НИОКР позволяет: исключить ошибки и устранить «слабые места» при проектировании нового изделия или модернизации существующего; сократить сроки разработки и реализации контрактов (экономия времени 35-40%); провести многократные испытания прототипа в цифровой среде без затрат на выпуск/доработку промежуточного изделия и проверить все возможные сценарии работы «что, если» на виртуальном производстве; уменьшить на 25-30% сроки вывода на рынок изделия с улучшенными параметрами; сократить на 20% издержки на ТОиР в процессе эксплуатации изделия.
«Однако без натурного прототипа нам все равно не обойтись: создав модель, мы не сможем проверить ее качество без ее валидации на реальном приборе, – подчеркнул Сергей Борисов-Смирнов. – Точность наших моделей составляет 95-97%».
Цифровые учебные стенды (тренажеры) дают возможность: разработать реалистичный тренажер на базе цифровых двойников технологических процессов с применением технологий VR (виртуальной реальности) и AR (дополненной реальности) для обучения правилам промышленной безопасности с целью предотвращения несчастных случаев; ускоренного обучения по специальностям и смежным профессиям, быстрого повышения квалификации; быстрой адаптации сценариев обучения.
Цифровая модернизация предприятия позволяет: быстро увеличить производительность производства на 30-35% без расширения штата и станочного парка; снизить уровень брака и отходов производства на 15-20%; сократить расходы на ТО на 20% – за счет сервиса оборудования по состоянию; уменьшить расходы на содержание персонала на 40% – за счет роботизации на опасных или вредных производствах; внедрить систему управления для рационального планирования и логистики на базе ERP, MES и OEE; организовать виртуальную (удаленную) пусконаладку, сократив количество выездов на объект на 30%.
К преимуществам цифровых решений от «ТВЭЛ» докладчик отнес: широкий спектр цифровых услуг; высокие технические компетенции в инжиниринге и производстве, а также по сертификации и лицензированию; поддержку работы с гостайной и различными степенями секретности; наличие высокой скорости разработки и точности получаемых параметров; возможность последующей эксплуатации; надежность конструкции и снижение вероятности ошибки; простоту модернизации и зарезервированный технологический запас.
Корпоративное управление
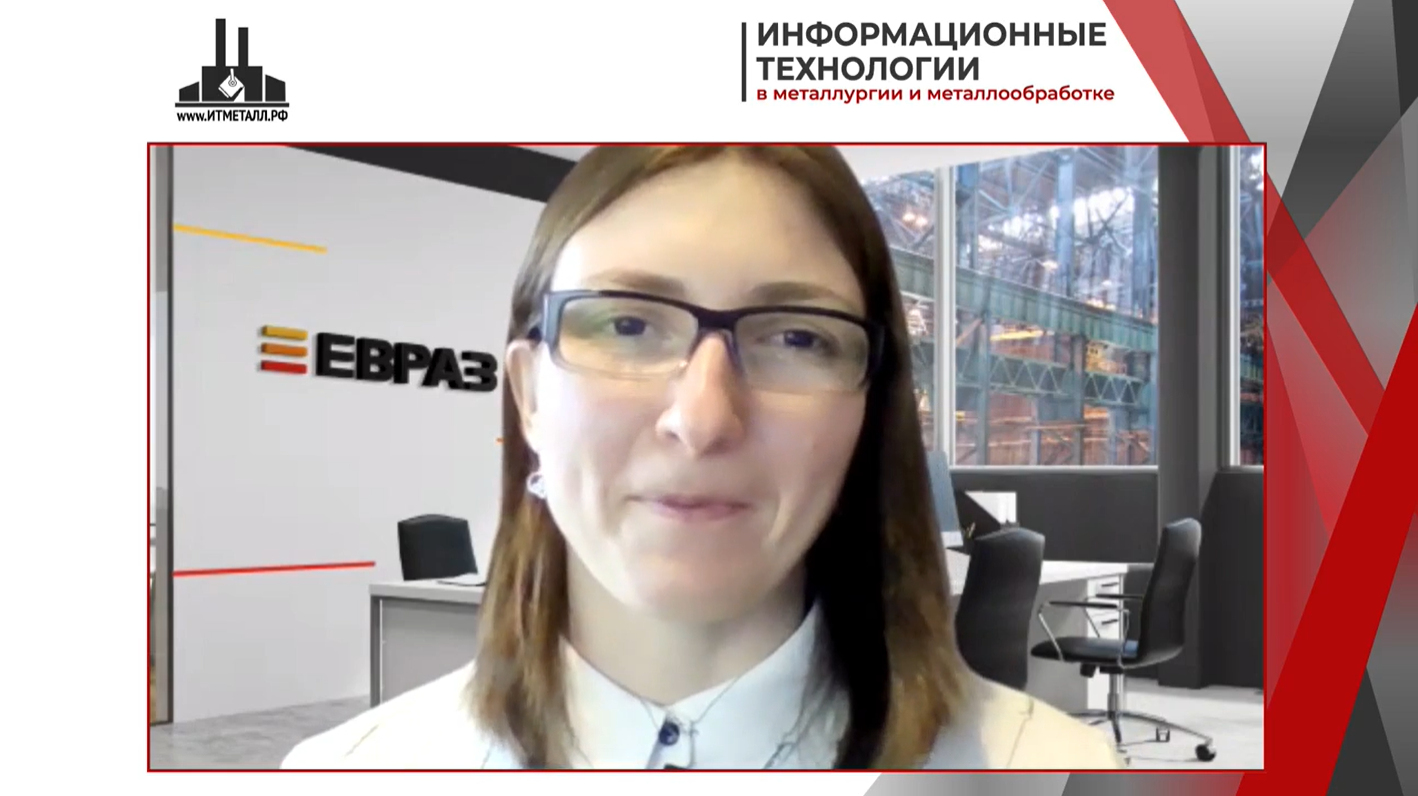
Ольга Падучева, руководитель ИТ-проектов, ООО «ЕвразХолдинг», представила доклад «Self Service аналитики в металлургии».
Чтобы компания могла и дальше оставаться в топ 10 Forbes, в ЕВРАЗ с 2018 года идет процесс цифровой трансформации. Как уточнила Ольга Падучева, в 2018 году даже не использовался сам термин «цифровая трансформация» – речь тогда шла о 24 локальных проектах. В 2019 году в компании велись 32 цифровых проекта. С конца 2020 и начала 2021 года ЕВРАЗ перешел к масштабному внедрению цифровых проектов: 2020 год – внедрено 68 цифровых проектов с годовым эффектом $20 млн; 2021 год – ведутся 150+ цифровых проектов с годовым эффектом $100+ млн. Цели цифровой трансформации: экономический эффект; решения на базе данных; позитивное влияние на ОТиПБ; снижение бюрократии; развитие и вовлеченность персонала; эффективное управление.
«Мы задались вопросом: как вытянуть все эти большие цифровые проекты, еще с учетом дефицита ИТ-специалистов (дата-сайентистов, бэкенд и фронтенд специалистов)? И одно из решений этой проблемы мы увидели в использовании таких простых ИТ-инструментов, как Low Code и No Code, подход SSA – создание нового ИТ-продукта силами инженеров аналитиков SDS (Citizen Data Scientist – «гражданский» аналитик данных, имеющий навыки по разработке прогнозных моделей, приложений) из подразделений».
Любая инициатива проходит несколько этапов ее реализации. На первом этапе сбора и агрегации данных собирается SSA-команда, в которую включается так называемый «гражданский» аналитик данных, имеющий навыки по разработке прогнозных моделей, приложений No Code, не относящийся к ИТ-подразделению компании. Их главная задача – очистить дата-сет, построить гипотезы и подтвердить существование корреляции между данными, построить визуализацию. На втором этапе строится модель, в которую затем загружается очищенный дата-сет. Делается это с помощью инструмента Azure Machine Learning, который умеет автоматически строить алгоритмы (вам не нужно знать коды программирования). Затем команда разрабатывает интерфейс, после чего выходит в подразделение и демонстрирует будущим пользователям прототип продукта. На третьем этапе (релиз) идет развилка. Если понятно, что с этим продуктом уже можно работать на стандартном ИТ-стеке и пользователей все устраивает, то продукт остается как разработка SSA-команды. Если у продукта есть недостатки, то нанимается продуктовая команда ИТ-специалистов, которая берет SSA-продукт и переводит его на стандартный ИТ-стек. Как видим, подход SSA позволяет экономить на привлечении ИТ-специалистов, причем, в обоих вариантах (во втором случае ИТ привлекаются лишь для доработки продукта). «По нашей оценке, SSA позволяет экономить до 30-50% на привлечении ИТ-специалистов», – считает Ольга Падучева. Подход SSA также позволяет развить «технолога будущего», который стоит плечом к плечу с ИТ-специалистом и позволяет ускорить процесс внедрения ИТ-продуктов.
«Мы понимаем, что для дальнейшего становления и развития Self-Service культуры в компании необходим кросс-дивизиональный Центр компетенций, объединяющий в себе экспертов по направлениям – для проведения обучения, консультирования, финальных обзоров моделей, сопровождения проектов», – считает Ольга Падучева.
Дальнейшие шаги по развитию подхода SSA в ЕВРАЗе предполагают: формирование дистанционного курса обучения SSA; создание внутреннего центра компетенций для преподавания и поддержки SSA-команд; развитие технологического стека (например, облачные сервисы, EVRAZ SSA фреймворк); определение роли ИТ в эксплуатации и поддержке SSA-проектов; расширение сфер применения инициатив (например, на этапе генерации идей).
Основной риск этого направления заключается в том, что люди, прошедшие обучение SSA, востребованы в «операционке», а не на решении аналитических задач.
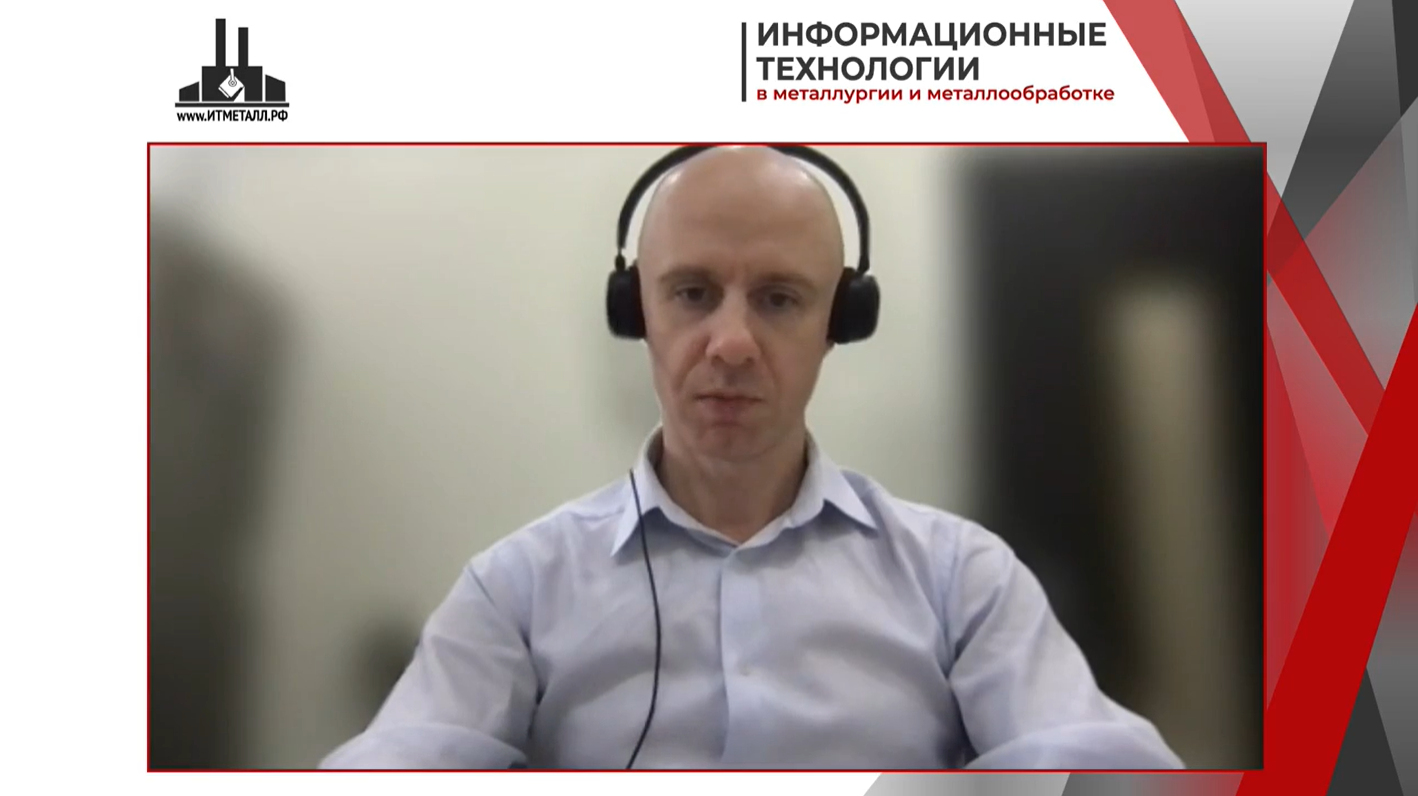
Дмитрий Карбасов, руководитель управления промышленного искусственного интеллекта ERG (Евразийская Ресурсная Группа), рассказал о расчете плановых сроков поставки.
Как пояснил докладчик, проблема состоит в том, что плановые сроки поставки (ПСП), вручную устанавливаемые закупщиками к каждой группе материалов ERG на основе их экспертизы, не всегда соответствуют фактическим срокам поставки. Соответственно, целью проекта было наладить автоматический расчет оптимальных или расчетных сроков поставки (РСП) по каждой группе материалов, статистически подтвержденных на основе анализа исторических данных. В результате выполнения этого проекта расчетные сроки поставки стали применятся в качестве замены плановым срокам поставки для обеспечения корректного планирования потребности в материалах и оперативного мониторинга закупочного процесса в целом.
Выполнение проекта включало в себя шесть основных этапов. 1) Сбор данных: сбор полного набора данных из исходных источников с заданной периодичностью; проверка полноты необходимых данных. 2) Очистка и оценка качества данных: фильтрация по условиям, заданных бизнесом; очистка данных (удаление дублей, пустых значений, некорректных записей, т.д.); проверка наличия и последовательности ключевых дат по заявкам. 3) Подготовка данных: расчет фактических сроков поставки по каждому материалу/заявке; разбивка материалов в укрупненные группы; присвоение группам материалов уровня доверия. 4) Расчет оптимального срока поставки (РСП): выделение доверительных интервалов по каждой группе материалов (верхняя и нижняя граница); расчет оптимального срока поставки внутри доверительного интервала. 5) Ретро-анализ и принятие решения: сравнение расчетных показателей с фактическими за наиболее актуальный период; принятое решение о выборе одного из РСП, либо сохранение ПСП. 6) Передача результата: сохранение результата в буферной базе данных; обеспечение возможности подтверждения/согласования результата ответственными лицами; передача рассчитанных РСП в SAP.
Уровень доверия принятия решения в качестве информативного признака определяет точность рассчитанного оптимального срока поставки в зависимости от количества точек наблюдений и степени их разброса внутри групп материалов. Чем выше уровень доверия, тем точнее рассчитанный срок поставки для данной группы материалов.
Уровень доверия определяется двумя ключевыми параметрами: количеством уникальных закупок и степенью разброса. Высокий и средний уровни доверия являются приемлемыми для корректного расчета оптимального срока поставки с учетом выбранного подхода. Материалы данных групп в целом чаще закупаются, по ним наблюдаются относительно стабильные сроки поставки, по сравнению с группами более низких уровней доверия.
Дмитрий Карбасов также заявил о том, что ERG готова обмениваться данными и делиться технологиями расчета плановых сроков с компаниями, которые заинтересованы в таком же проекте у себя. Докладчик предложил следующий порядок взаимодействия и объем передаваемых данных: принципиальное согласование на уровне руководства компаний; формирование рабочих групп с вовлечением ИТ и бизнеса; согласование требований и критериев оценки; согласование форматов обмена информацией; формирование и передача согласованного пакета данных; реализация тестового сценария силами ERG; оценка результата на уровне рабочих групп; презентация руководству и планирование дальнейшего развития.
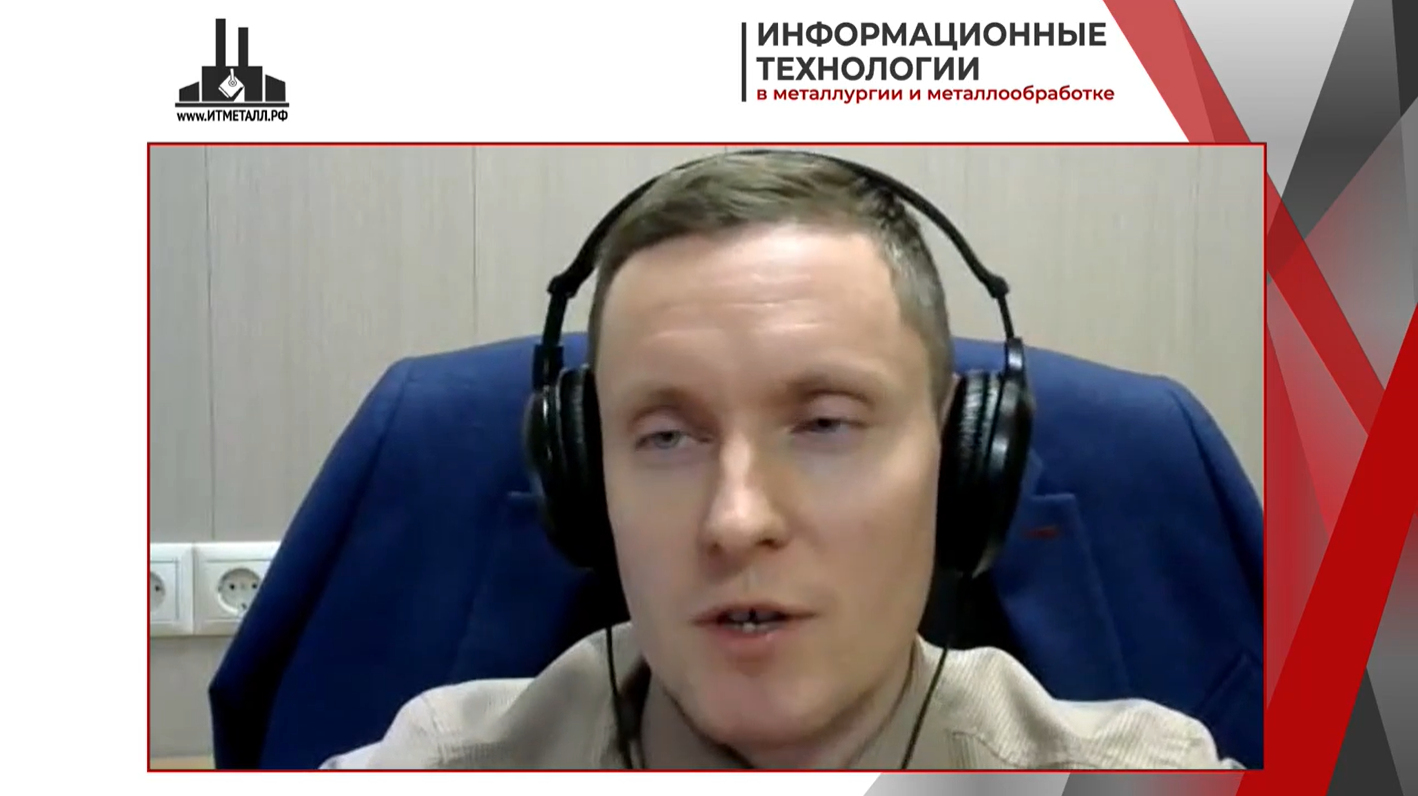
Роботизация бизнес-процессов на ПАО «ММК» была представлена в докладе Сергея Красильникова, ведущего специалиста Центра компетенций RPA и инноваций, ПАО «ММК».
В 2018 году был запущен первый пилотный проект, который стал фундаментом RPA для Группы ММК и подтвердил работоспособность этого ИТ-инструмента по автоматизации. В следующем 2019 году стартовал масштабный проект по выявлению бизнес-процессов, подходящих для роботизации с помощью RPA: «Тогда мы поняли, что к выбору бизнес-процессов для роботизации необходимо подходить очень скрупулезно». Была проведена роботизация порядка 70 процессов. В Центре компетенций RPA поняли, что они могут проводить подобную работу не только в «ММК», но и за пределами компании. Тогда же были предприняты попытки вывести на рынок RPA в качестве услуги.
В 2020 году было роботизировано уже более 100 бизнес-процессов: роботизация пошла во всех функциональных направлениях, начали делать проекты для крупных заказчиков. В 2021 году в «ММК» началась массовая роботизация, а Центр компетенций RPA был выведен в отдельную компанию и начал довольно успешно коммерциализировать свои услуги в области RPA вне Группы ММК, предлагая заказчикам комплексные проекты (RPA под ключ): Process Discovery, Task Mining, Task Capture, Process Mining, процессная аналитика. В Центре компетенций RPA был взят курс на гиперавтоматизацию.
К настоящему времени роботы в «ММК» отработали уже более 385 000 часов. Решения RPA применяются в самых различных сферах: 1) экономика и финансы – ежесуточное формирование отчетов и рапортов, внесение информации из полисов ОСАГО, выгрузка банковских выписок из клиент-банков; 2) снабжение и логистика – открытие торгов на ЭТП, поиск актуальных документов на федеральном портале проектов нормативных правовых актов, проверка статусов груза; 3) бухгалтерский учет – формирование актов сверки (РСБУ и МСФО), ежедневный контроль незакрытых авансов, выявление и исправления расхождений данных в различных учетных ИС; 4) персонал и кадры – подготовка распоряжений и соглашений, оформление временных переводов и совмещений, подготовку справок 2НДФЛ и других справок.
Самый масштабный бизнес-процесс в «ММК», который удалось роботизировать, учет и оплата поставок металлолома – стратегический для комбината процесс. Метрики этого процесса впечатляют: 150 вагонов в сутки, 36 000 документов в месяц, 3 000 000 тонн в год. В этом процессе задействованы 5 ИТ-систем и приложений: 2 500 операций в день, 100 500 млн кликов в год. В данном процессе выделены 9 функциональных направлений. «В пиковые моменты, когда объемы поставок достигают своего максимума, RPA-роботы замещают труд 32 сотрудников», – подчеркнул Сергей Красильников.
Роботизированный процесс учета и оплаты поставок металлолома включает в себя следующие этапы: сбор данных от поставщиков, проверка факта отгрузки, расчет суммы авансов, подтверждение менеджером, формирование платежа, загрузка в банк, запрос подтверждения платежа, подписание платежа в банке, мониторинг состояния поставки, обработка счетов-фактур, формирование платежа, подтверждение платежа. Здесь имеется множество рутинных операций, подверженных простой алгоритмизации, – они требуют внимательности, которую RPA-роботы, естественно, обеспечивают лучше человека. Там, где требуется элемент ответственности (подписание документов), задействованы люди: подтверждение заказа менеджером, подписание платежа в банке, подтверждение платежа.
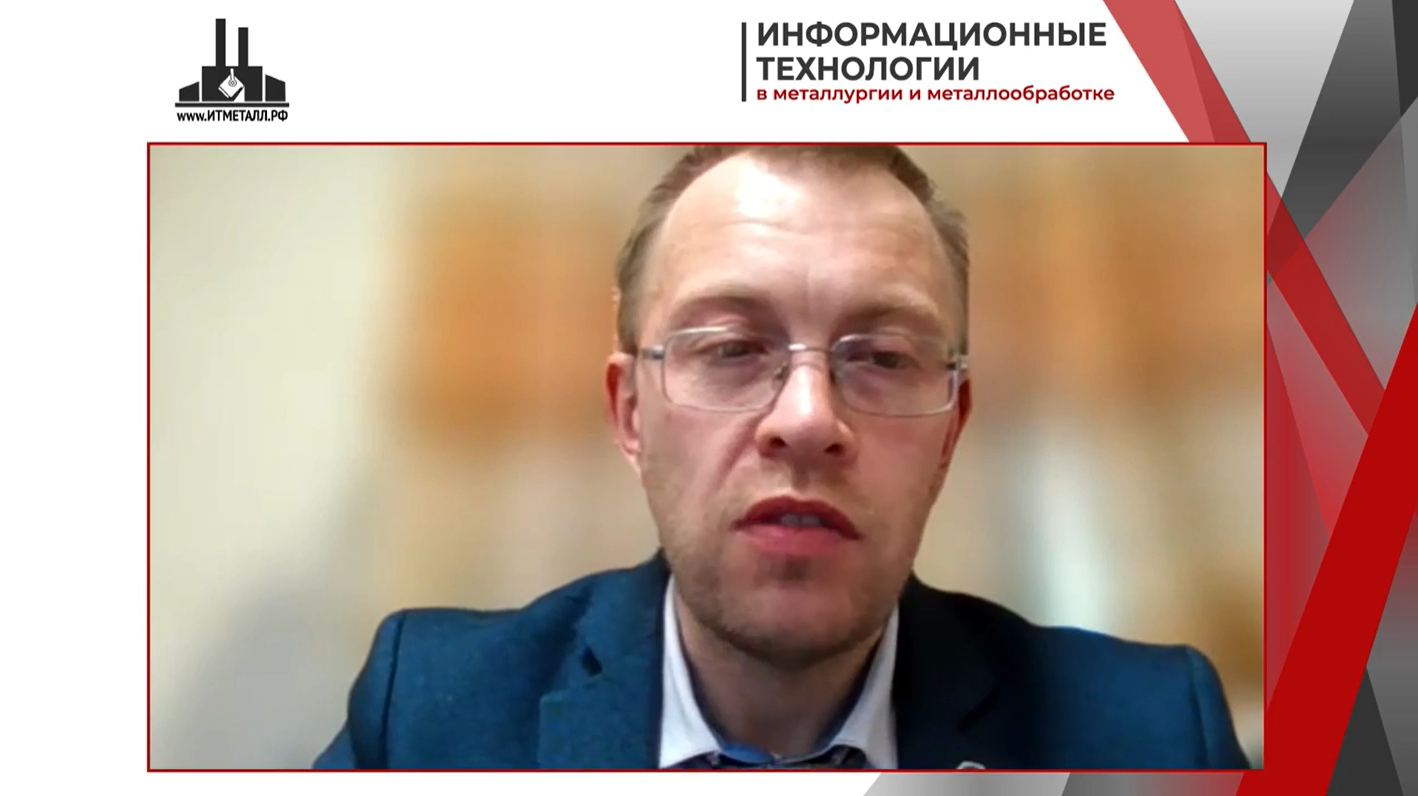
Артем Губайдуллин, заместитель руководителя по реализации проектов в области Индустрии 4.0 ОАО «ММК-МЕТИЗ», выступил с докладом на тему «Современные методы обеспечения безопасности персонала «ММК-МЕТИЗ» при помощи системы искусственного интеллекта и комплекса машинного зрения».
Как отметил докладчик, идея использования систем машинного зрения в ОАО «ММК-МЕТИЗ» возникла как результат грамотного подхода специалистов по охране труда к требованиям по обеспечению безопасности работающего персонала.
Артем Губайдуллин представил типовую платформу видео аналитики, применяемую в одном из цехов «ММК-МЕТИЗ»: захват изображения высокой четкости (фото и видео файлы); обработка изображения (разбор видео на кадры, подготовка, нарезка, сжатие); типизация объектов и их обнаружение (на основе систему искусственного интеллекта и машинного обучения); постобработка изображения; результирующее действие, которое выполняет либо автоматизированная система, либо какой-то исполнительный механизм.
«Идея применения системы обнаружения персонала возникла после того, как в цехе стали строить заграждающие устройства (по технике безопасности), которые со временем даже начали мешать основной деятельности – занимать складские площади, мешать проходу персонала между оборудованием и т.д. Поэтому было принято решение заменить эти неудобные перегородки системой компьютерного зрения, которая позволит оповещать персонал цеха свето-шумовой сигнализацией при захождении в опасную зону», – пояснил Артем Губайдуллин. Решение разбито на две подсистемы: одна занимается обнаружением людей в опасной зоне; вторая подсистема распознает наличие (отсутствие) на персонале цеха систем индивидуальной защиты.
От внедрения этой системы машинного зрения в «ММК-МЕТИЗ» ожидают снижения травматизма персонала при производстве работ; повышения трудовой дисциплины в части правильности применения средств индивидуальной защиты за счет: обеспечения обнаружения до 100% случаев нарушений требований ОТ и ТБ; мгновенного оповещения заинтересованных служб о случаях нарушений. Артем Губайдуллин также обратил внимание на такой аспект, как поддержание имиджа «ММК-МЕТИЗ» в глазах персонала как современной инновационной компании в эпоху цифровой трансформации. А главное, система позволяет организовать выполнение требований Указа Президента Российской Федерации от 06.05.2018 года № 198 «Об Основах государственной политики Российской Федерации в области промышленной безопасности на период до 2025 года и дальнейшую перспективу» и других нормативных актов.
Перспективы развития системы машинного зрения предусматривают следующие три направления. 1) Интеграция системы с элементами АСУ ТП оборудования – для ранжирования событий необходимо выполнить доработку системы распознавания персонала в опасных зонах на предмет определения фактического состояния опасного производственного оборудования – в работе/не в работе. 2) Установка дополнительных купольных камер – повышение точности детектирования нахождения персонала в опасной зоне позволит выполнить доработку системы за счет 3D-съемки. В настоящий момент камеры расположены по периметру технологического оборудования и нахождение людей в опасных зонах происходит путем трансформации двухмерного изображения в всевдо-3D, что действует не всегда корректно. 3) Интеграция с системой распознавания лиц – связь системы с кадровой системой предприятия позволит определять, находится в опасной зоне сотрудник предприятия или сторонней организации.
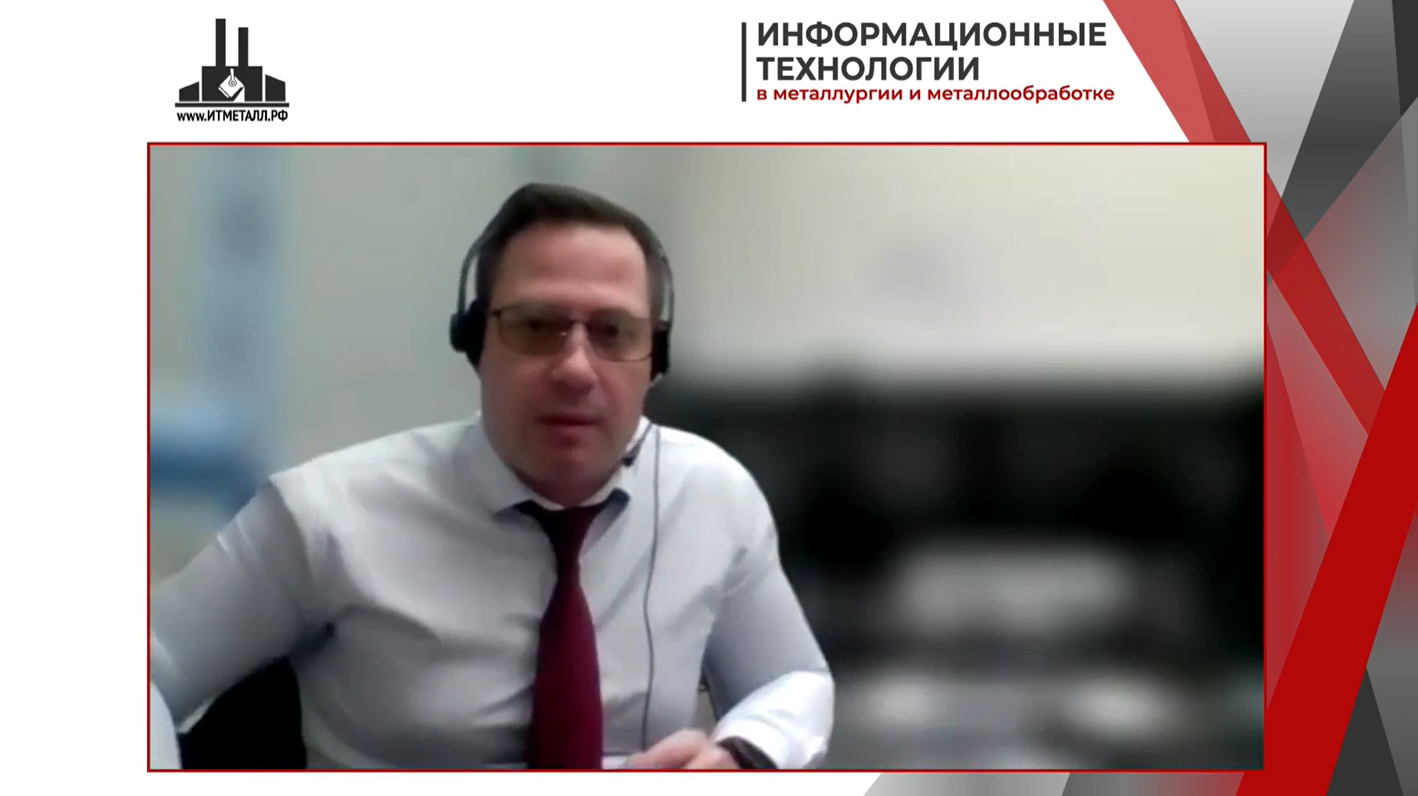
Александр Севостьянов, начальник управления информационной безопасности СЭБ ПАО «ТМК», проанализировал проблемные вопросы и особенности защиты ИТ-проектов цифровизации в металлургии.
«Цифровой двойник в промышленности – это возможность, которая позволит получить устойчивое конкурентное преимущество на рынке с использованием современных цифровых технологий и алгоритмов, что обязательно подлежит защите от несанкционированного доступа и шпионажа», – считает Александр Севостьянов.
Докладчик, основываясь на своем опыте работы, выделил следующие основные объекты защиты: ИТ инфраструктура проекта (сервера, сетевое оборудование, пользовательские рабочие станции); каналы передачи данных (нужно шифрование); алгоритмы обработки данных (формулы, расчеты, программный код); проектная информация (ТЗ, ТКП, ТЭО); результаты исследований (НИОКР, НИР, отчеты по испытаниям и т.д.); СУБД проекта; удаленные рабочие места и каналы подключения извне.
Говоря об особенностях обеспечения ИБ цифровых проектов, Александр Севостьянов затронул юридическую сторону вопроса. Распоряжением Правительства РФ от 28 июля 2017 года №1632 р утверждена программа «Цифровая экономика Российской Федерации», согласно которой, основными сквозными цифровыми технологиями являются: большие данные; нейротехнологии и искусственный интеллект; системы распределенного реестра ; квантовые технологии; новые производственные технологии; промышленный интернет; компоненты робототехники и сенсорика; технологии беспроводной связи; технологии виртуальной и дополненной реальностей (предусматривается изменение перечня таких технологий по мере появление и развития новых технологий).
Правовые рамки защиты «Цифровых двойников» основываются на следующих звеньях. Качественная договорная работа (надо предусмотреть все острые моменты по разделению зон ответственности участников). Обязательное подписание NDA со всеми участниками (подрядчиками) проекта (включая работников). Определение статуса проекта: 1) «ноу хау» (секрет производства); 2) интеллектуальная собственность в виде РИД, согласно п.п.2, 3 п.1 ст.1225 ГК РФ, часть четвертая. Определение режима защиты: «коммерческая тайна», т.е. 98 ФЗ.
«Мало кто задумывается о том, что любой цифровой актив, проект, который реализуется на предприятии, – это интеллектуальная собственность компании, ее актив, который необходимо защищать не только на техническом уровне, но и на юридическом», – особо подчеркнул Александр Севостьянов.
Большое внимание докладчик уделил технической стороне вопроса защиты цифровых проектов. Во-первых, он указал на определение конфигурации ИТ-инфраструктуры проекта: требуемые вычислительные мощности и их характеристики; определение областей; хранение данных (запас в минимум 30% по хранению); определение ИС и средств; обработка данных (SCADA, PLC и т.д.), с которых поступают информационные потоки и собираются данные; определение средств обработки и моделирования всех процессов, включая пользовательские рабочие станции.
Построение безопасной конфигурации цифровых проектов предусматривает следующие направления работы: изолирование серверов хранения и обработки данных проекта от корпоративного сегмента сети (выведение серверов в отдельный сегмент, либо в DMZ) с разграничением доступа по пользователям; установка средств шифрования данных на серверах хранения; создание шифрованных каналов связи между серверной и пользовательским частями; применение средств антивирусной защиты; блокирование свободного выхода в интернет и к портам USB разработчикам проекта путем предоставления им отдельных выделенных рабочих станций (применение не сетевых машин); установка средств внутреннего видеонаблюдения, СКУД (системы контроля и управления доступом).
Основной постулат защиты цифровых проектов, имеющих статус «ноу хау», заключается в том, что вся обработка, хранение и оборот данных должны осуществляться внутри ИТ-контура самой организации с минимальным применением решений удаленной работы для разработчиков и представителей подрядных организаций в изолированном сегменте сети.
Производство
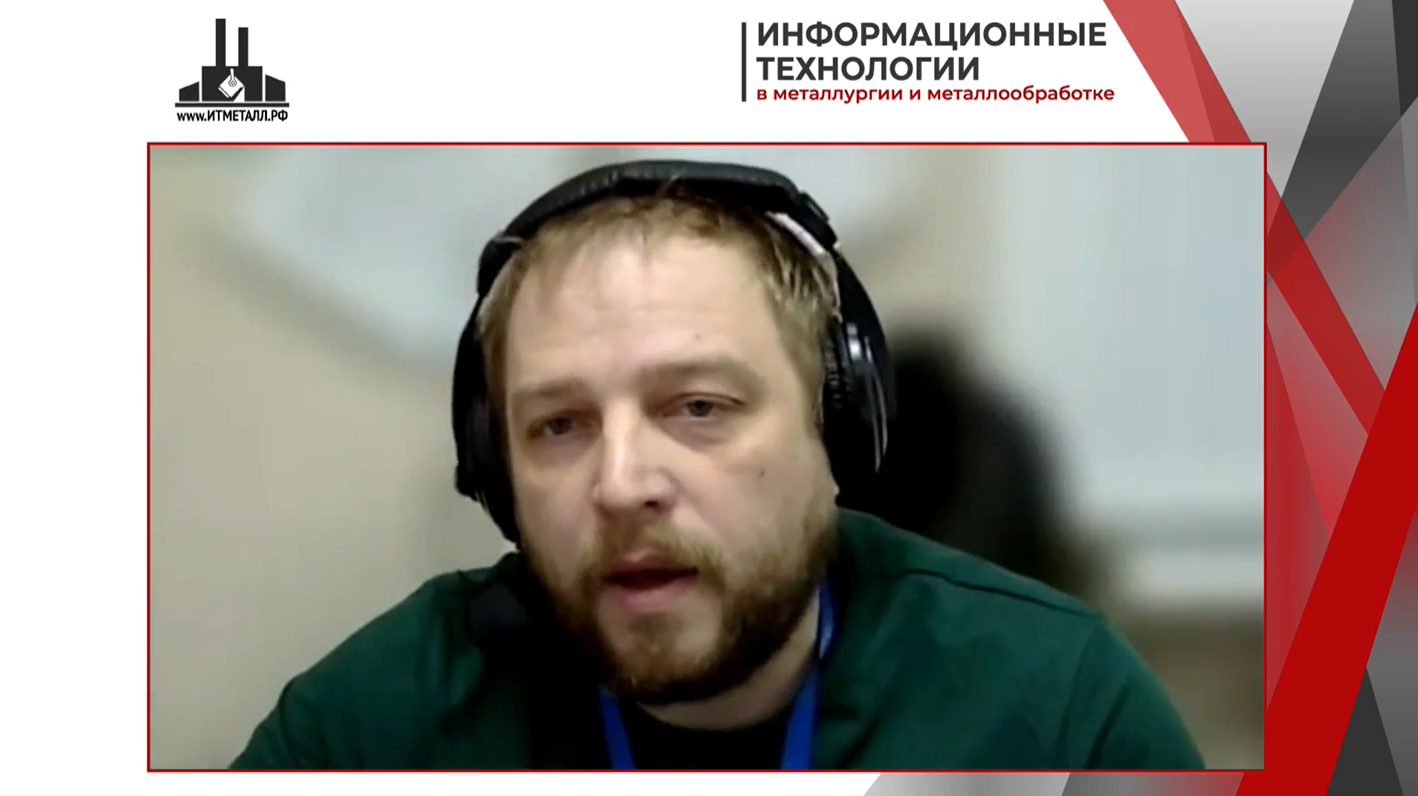
Опытом внедрения системы мониторинга парка станков на металлообрабатывающем или обеспечивающем металлургическом производстве поделился Константин Ковальчук, руководитель ИТ-службы «ВолгаСтальПроект».
Как пояснил докладчик, инициатива по созданию системы мониторинга загрузки станков поступила в Ит-отдел от руководства компании. В ИТ определили список оборудования, которое необходимо мониторить, задали список данных, которые нужно было получать, и рассчитали бюджет проекта.
Особенность проекта заключалась в том, что возникла необходимость подключаться к простому оборудованию, которое не содержало в себе микроэлектроники (чипов и пр.), а мониторит его надо было. В этом случае приходилось подключаться непосредственно к самому мощному двигателю оборудования и снимать данные через трансформаторы тока.
Были рассмотрены различные подрядчики, предоставляющие соответствующие системы, но для «ВолгаСтальПроекта» эти решения оказались чрезмерно дорогими, поскольку на каждый станок необходимо было бы подвешивать по дополнительному терминалу. В результате, было принято решение идти своим путем: проект SCADA обеспечил низкую стоимость решения, неплохую масштабируемость и простоту управления.
На каждый станок повесили трансформатор тока, соединенный по RS485 с контроллером, который, в свою очередь, подключается к сети предприятия и передает данные либо в облако, либо на сервер SCADA (в зависимости от поставленных задач). Новая система позволяет мониторить оборудование и поставлять отчеты – суточные и более подробные.
«Тем не менее, любую систему можно обмануть, – поделился своим опытом Константин Ковальчук, – поэтому необходимо дублировать системы, например, внедрять систему видеонаблюдения за станочным парком».
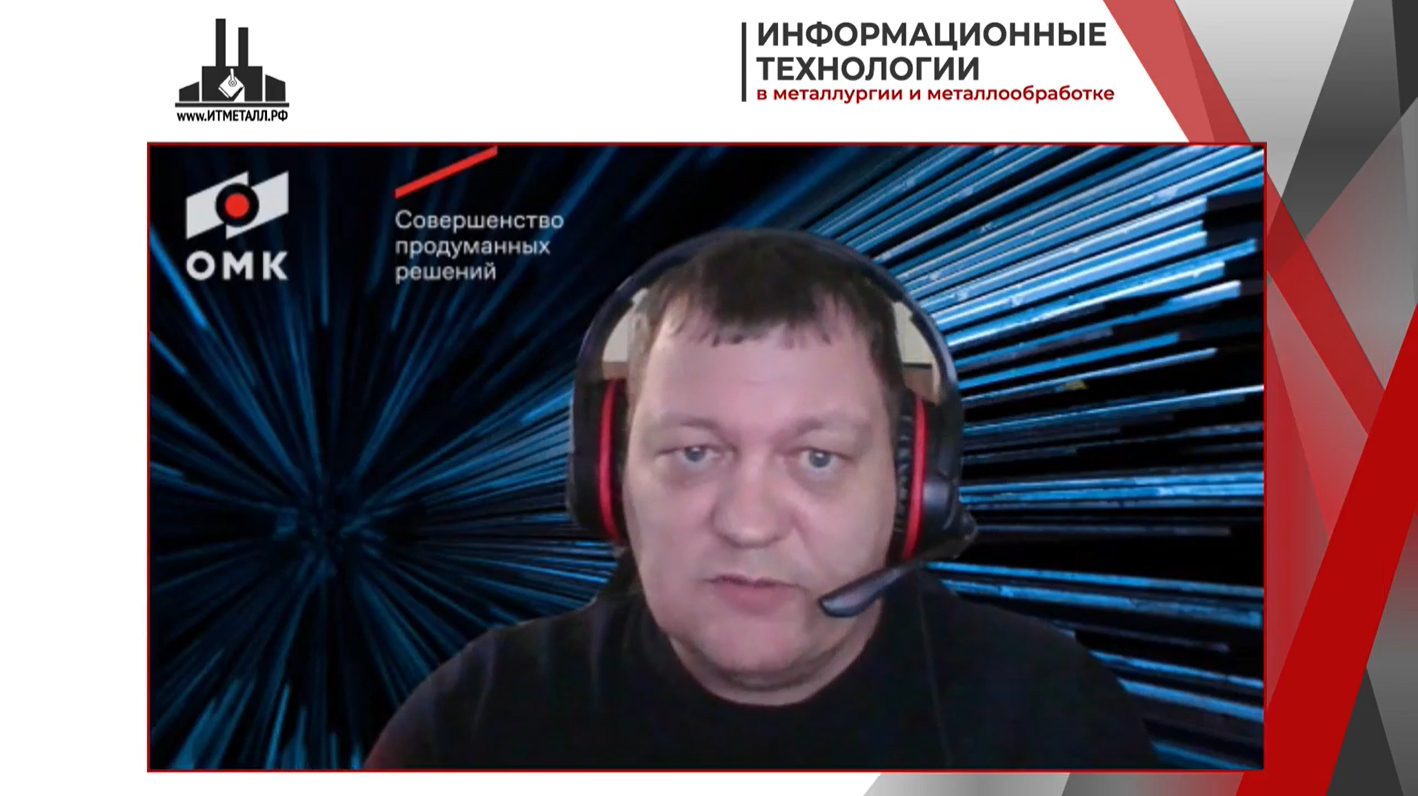
Развитие средств автоматизации визуального и измерительного контроля на предприятиях ОМК было представлено в докладе Максима Шамшина, руководителя проектов, АО «Выксунский металлургический завод».
Визуальный и измерительный контроль (ВИК) – это один из методов неразрушающего контроля, который, в первую очередь, основан на возможностях зрения, объект контроля исследуется в видимом излучении. Контроль проводится с использованием простейших измерительных средств таких как: лупа, рулетка, УШС, штангенциркуль и т.д. С его помощью можно обнаружить: коррозионные поражения, трещины, изъяны материала и обработки поверхности и пр.
Визуальный и измерительный контроль также проводят и при помощи оптических приборов, что позволяет значительно расширить пределы естественных возможностей человеческого глаза.
Основные проблемы «ручного» метода ВИК заключаются в следующем: субъективность оценки качества; человеческий фактор; невозможность проведения в экстремальных и опасных условиях; низкая скорость контроля.
Целями проекта по развитию средств автоматизации ВИК были: устранение проблем «ручного» метода ВИК-контроля; повышение эффективности инвестиций компании; повышение эффективности производства продукции.
Были выделены четыре основных уровня детализации проработки задачи: 1) ценность – определяет, какую конкретную пользу мы получаем от внедрения цифровых решений в производстве; 2) решение – способ решения конкретной производственной задачи для достижения ценности; 3) технология – технология построения решения производственной задачи; 4) алгоритмы – алгоритмы и методы получения и обработки данных.
Развитие внутри команды проекта своего центра компетенций, позволило снизить стоимость получения решений за счет покупки на рынке не готовых решений, а лишь технологий решений задач. Также некоторые технологии решений разрабатываются самостоятельно. Все это приводит к росту эффективности внедрения решений.
Докладчик указал на основные решаемые задачи в проекте: контроль качества поверхности (компьютерное зрение на основе 2D-модели поверхности, компьютерное зрение на основе 3D-модели поверхности, компьютерное зрение на основе 2D+3D-модели поверхности); измерение геометрических параметров (измерения на основе 3D-облака точек или лазерная триангуляция, фотограмметрия, роботизированные контактные измерения); детекция и распознавание объектов (компьютерное зрение на основе 2D-модели поверхности + видеоаналитика, компьютерное зрение на основе 3D-модели поверхности + видеоаналитика); температурные изменения (термография).
Применение ВИК Максим Шамшин показал на конкретных примерах: повышение качества контроля поверхности стальной полосы на ЛПК при помощи свёрточных нейронных сетей; автоматический визуальный контроль качества поверхностей на муфтах; автоматизированный контроль за утечками на установке гидроиспытаний труб; контроль геометрических параметров труб после сварки, применение метода термографии сварного шва для оценки качества процесса сварки; контроль качества поверхности оправок непрерывного стана ТПЦ.
«Перед нами стоит задача – убрать человека непосредственно из зоны контроля и заместить его математической моделью», – заявил Максим Шамшин.
Первые выводы по работе конференции
Дмитрий Корешков, заместитель генерального директора издательского дома «Коннект», от лица организаторов мероприятия поблагодарил докладчиков и всех его участников. Он подвел предварительные итоги конференции, отметив, в частности, что в этом году много внимания было уделено тематике цифровых двойников, поскольку специалисты отрасли видят большой потенциал этой технологии.
Специалисты отрасли также продемонстрировали интерес к тематике искусственного интеллекта, использованию ИИ в машинном зрении для контроля качества продукции и в целях обеспечения безопасности на производстве. Развивается тема роботизации бизнес-процессов, характерная, впрочем, не только для металлургии, но и для любых крупных предприятий России.
Особо стоит отметить появление сразу в нескольких докладах такой становящейся все более популярной темы, как решения на базе Low-Code, в связи с чем отмечается рост компетенций в сфере ИТ на предприятиях отрасли, тенденция сращивания (в хорошем смысле слова) ИТ-специалистов и технологов производства.
Архиважной темой, заслуживающей отдельного мероприятия, является информационная безопасность: ряд спикеров обозначили болевые моменты, связанные с информационной безопасностью на предприятиях металлургии.
Еще одна важная тема, прошедшая красной нитью через выступления ключевых спикеров, – это стремление, по возможности, исключить человеческий фактор из технологических процессов на производстве, автоматизация большинства рутинных операций.