3 декабря 2020 г. состоялся Второй международный отраслевой форум «Информационные технологии в металлургии и металлообработке», организованный Издательским домом «КОННЕКТ». В этом году мероприятие прошло в онлайн-формате. К работе форума подключились представители нескольких зарубежных стран: Казахстана, Узбекистана, Республики Беларусь, а также специалисты столичных и региональных предприятий металлургии и горнодобывающей промышленности и др. Партнерами форума выступили компании «Mail.ru Цифровые технологии», МТС, АМТ-ГРУП и SKYMEC. В работе форума приняли участие 232 специалиста.
Корпоративная автоматизация
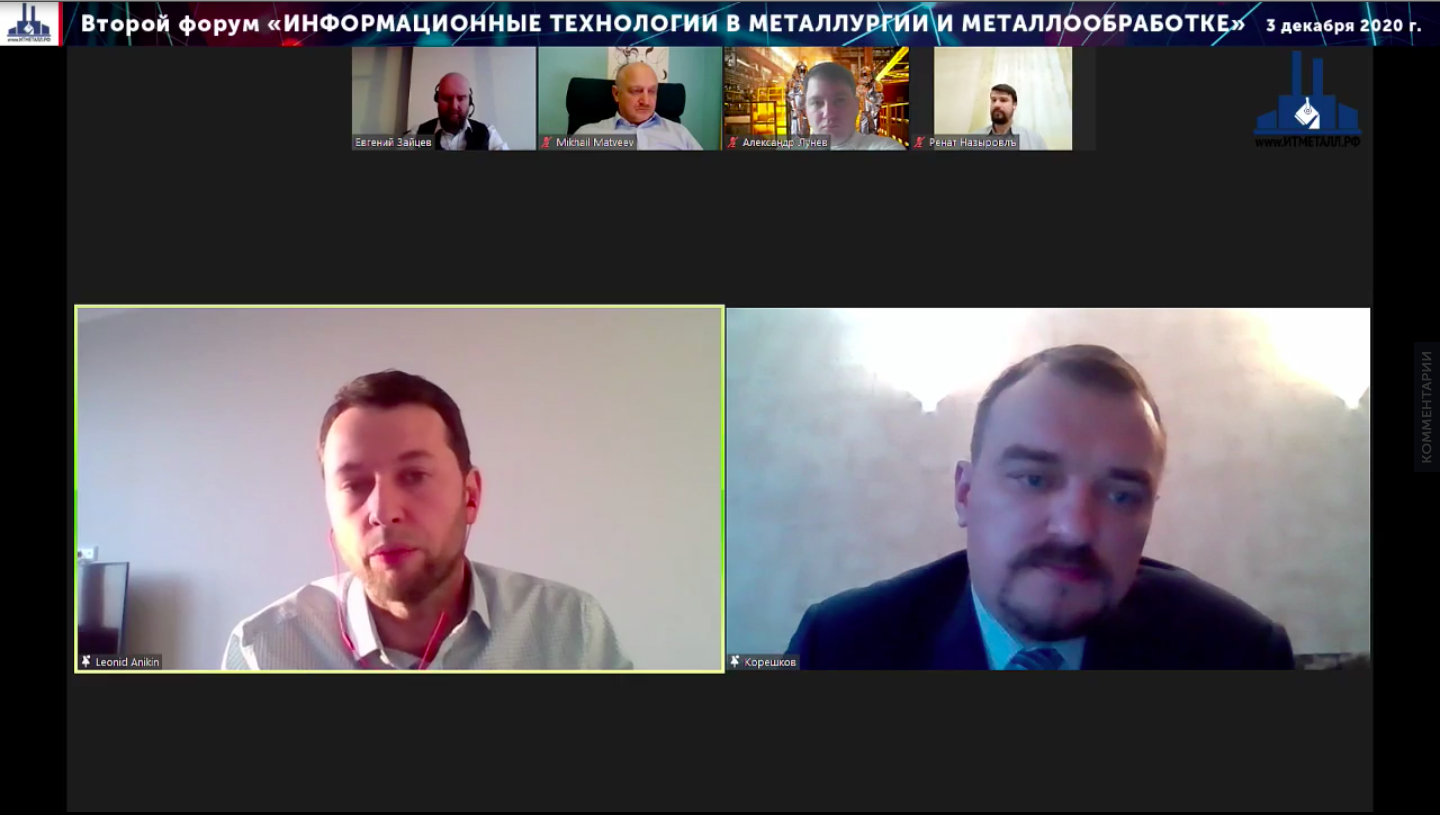
Открылся форум панельной дискуссией, посвященной наиболее актуальным вопросам цифровизации металлургической отрасли. Ее модератором стал заместитель генерального директора ИД «КОННЕКТ» Дмитрий Корешков. В обсуждении приняли участие представители разработчиков ИТ-решений: Леонид Аникин, директор по развитию бизнеса «Mail.ru Цифровые технологии», Михаил Матвеев, директор центра промышленной автоматизации МТС, а также представители металлургических компаний: Евгений Зайцев, директор по информационным технологиям АО «Загорский Трубный Завод» (ЗТЗ), Александр Лунев, начальник отдела ПАО «Челябинский трубопрокатный завод» (ЧТПЗ), Ренат Назыров, директор департамента «Сквозная автоматизация» Объединенной компании РУСАЛ, и Андрей Новиков, заместитель начальника Управления автоматизации ОАО «Белорусский металлургический завод – управляющая компания холдинга белорусская металлургическая компания».
Важной темой на любом промышленном предприятии является корпоративная цифровизация: взаимодействие предприятия с контрагентами и рынком, роботизация типовых задач при помощи RPA, анализ больших данных. Поэтому в панельной дискуссии один из вопросов был посвящен теме роботизации офисной активности с помощью RPA. В частности, Евгений Зайцев отметил, что для ЗТЗ наиболее интересной задачей корпоративной автоматизации является вопрос взаимодействия с контрагентами с помощью юридически значимого электронного документооборота.
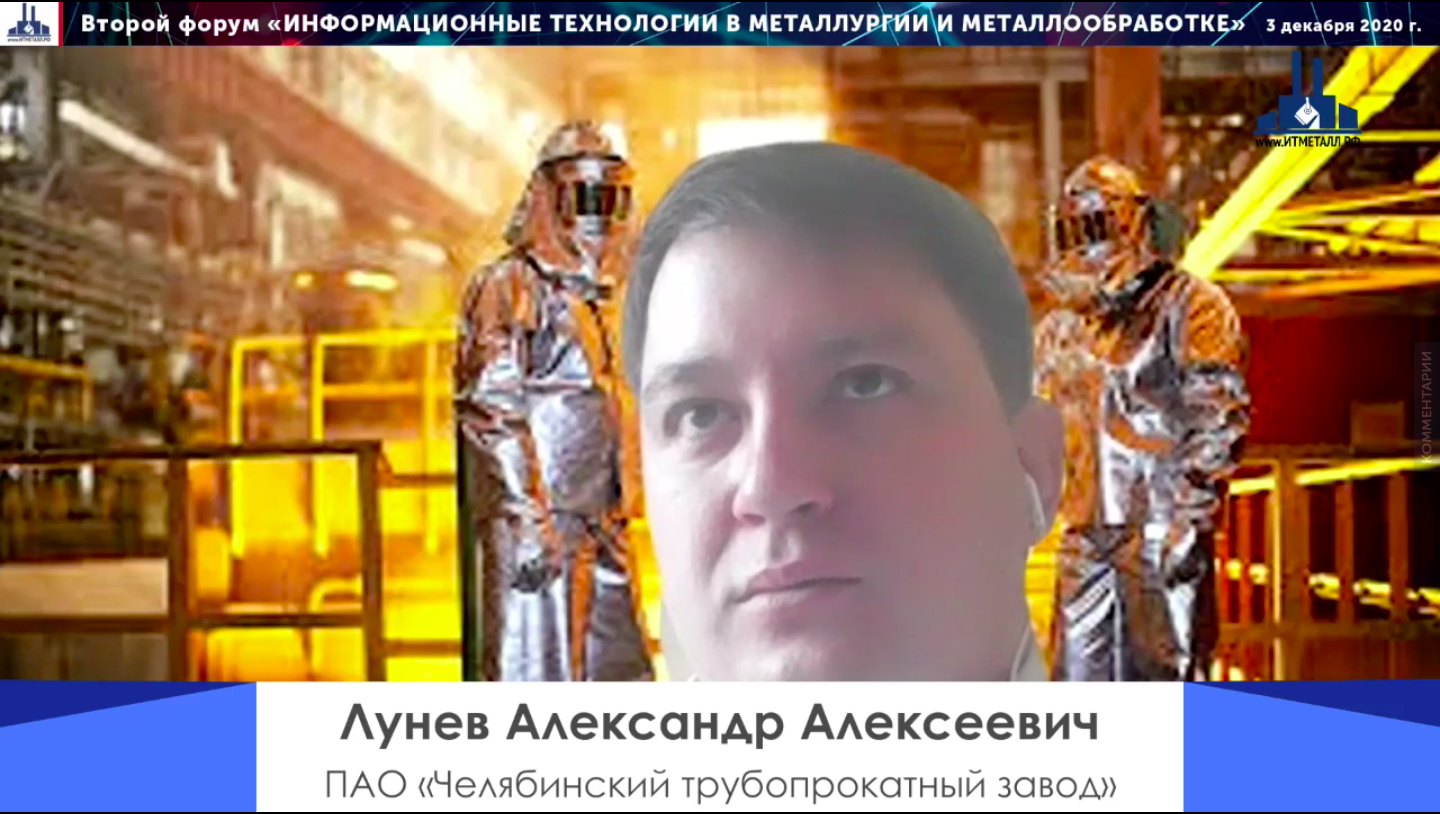
Александр Лунев так описал ситуацию в ЧТПЗ: «По продуктам RPA и корпоративной автоматизации у нас в компании есть точечные решения. Например, зайти на какой-то сайт и получить от него оперативную информацию или проверить появление нового документа». В то же время целенаправленной стратегии у ЧТПЗ по внедрению технологий RPA пока нет.
Разработчики цифровых сервисов сейчас занимаются интеграцией отдельных решений для офисных сотрудников в единую панель – кабинет офисного сотрудника. Это путь перехода к цифровым помощникам и электронному документообороту. «В текущем году больше удаленной работы и меньше встреч, – отметил Леонид Аникин. – Кроме того, наблюдается удешевление дорогих технологий анализа больших данных и предиктивной аналитики. Мы сделали ставку на интеграцию всех сервисов в виде единого цифрового помощника, который стал естественным интерфейсом для доступа к корпоративным системам, что важно для промышленности в плане цифровизации сотрудников». Занималась компания и построением корпоративных платформ для управления данными, причем как недорогого облачного продукта, так и внутрикорпоративного решения, которое может быть развернуто на территории заказчика. Леонид Аникин отметил, что особенности этого года привели к дополнительному росту в 10–15% по всем направлениям облачного бизнеса.
Искусственный интеллект
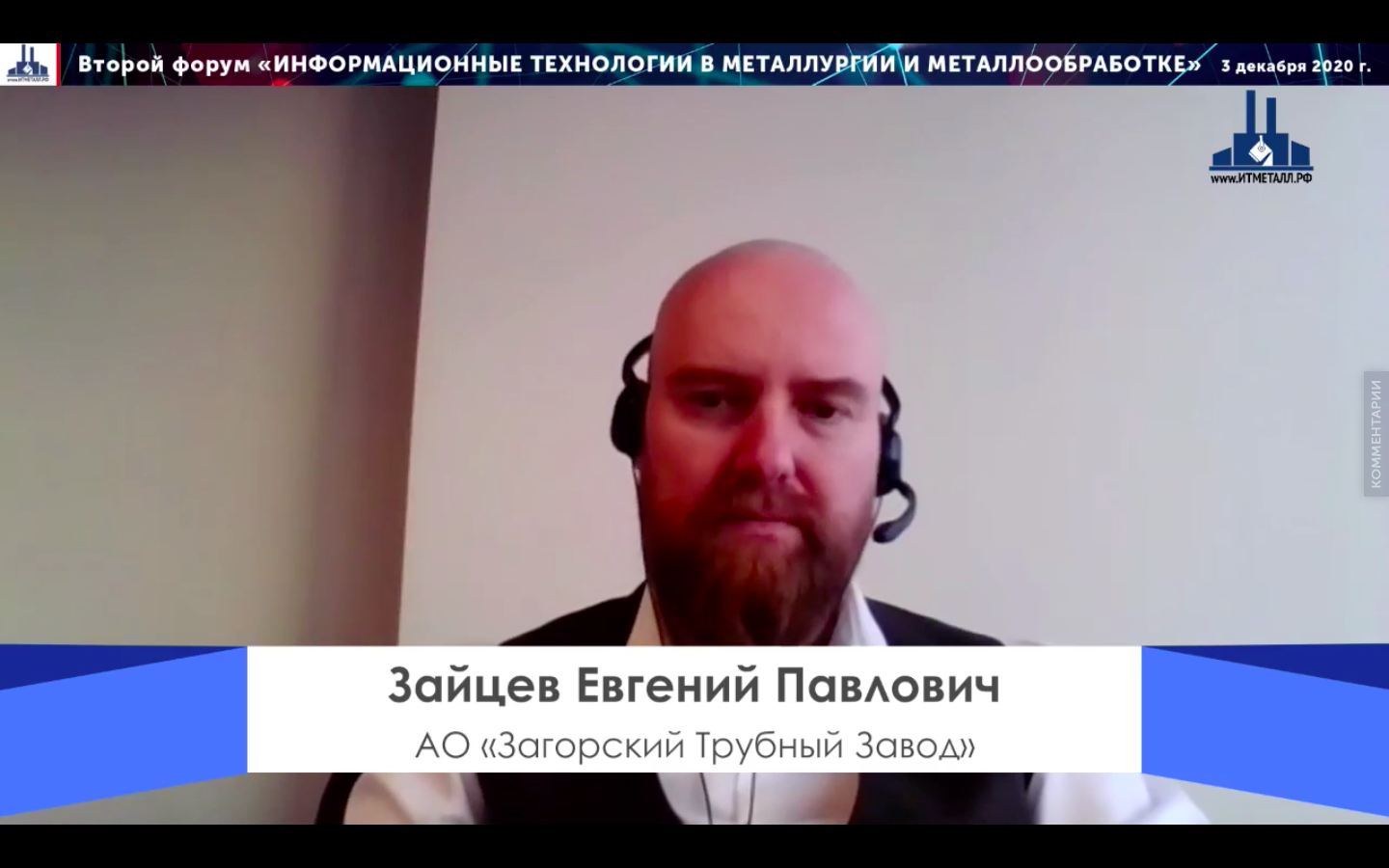
Существенная часть цифровой трансформации промышленных предприятий выполняется с помощью технологий искусственного интеллекта – они также обсуждались в ходе панельной дискуссии форума. «Машинное зрение – наиболее понятное и естественное применение методов искусственного интеллекта и нейросетей в металлургии, – отметил Евгений Зайцев. – У нас был пилотный проект, когда мы одну и ту же задачу делали на нейросети и на математической модели. Результаты получились примерно одинаковые, хотя нейросеть меньше зависит от погрешностей видео». Впрочем, технологии распознавания видео и изображений уже используются на большинстве металлургических заводов, где есть много вариантов применения машинного зрения: оценка качества металла, отслеживание труб с помощью нескольких камер, распознавание номеров вагонов и автомобилей и др. В принципе, машинное зрение можно использовать везде, где человек должен стоять и контролировать процесс.
В частности, Евгений Зайцев рассказал о внедрении на ЗТЗ технологии погрузки труб в вагоны, при которой система машинного зрения распознает, сколько труб в реальном вагоне содержится, и проверяет, соответствует ли это количество накладной. «Раньше за этим следили люди, – пояснил Евгений Зайцев. – Сейчас мы поставили лазерный датчик, данные с которого передаются в нейросеть. Она определяет схему укладки и обеспечивает подсчет погруженных труб. Затем посылается запрос в SAP для проверки правильности погрузки». Частным металлургическим компаниям приходится считать все затраты в новые технологии, и если отдачу от их внедрения подтвердить трудно, то в такой проект вряд ли кто будет вкладывать деньги.
Александр Лунев отметил и другое направление эффективного использования искусственного интеллекта – предиктивную аналитику. «У нас технологии искусственного интеллекта развиваются около трех лет, – пояснил он. – Мы используем как предиктивную аналитику и оптимизацию, так и технологии машинного зрения, которые активно внедряются в электросталеплавильном производстве в Первоуральске. Уже несколько лет развиваем специальный продукт «Помощник сталевара» – ранее это был инструмент для экономии ферроматериалов, сейчас спектр его применения расширен на другие технологические переделы. В нем уже используется уже около 20–30 моделей машинного обучения».
По словам Александра Лунева, сложности возникают при разработке таких предиктивных моделей, в которых на вход может подаваться от 300 до 500 параметров, а количество обрабатываемых показаний исчисляется миллионами. Причем технологические данные не всегда достаточно чисты для очевидного выявления трендов, что ухудшает качество предсказания моделей. В этом случае основное время для решения задачи уходит на взаимодействие с предметным специалистом, чтобы понять, как данные очищать, какие условия нужно создать, чтобы искусственный интеллект мог выявить суть проблемы. К тому же даже в современных цехах, оснащенных самыми разнообразными датчиками, далеко не все показания, полученные от датчиков, сохраняются в базы данных для последующего анализа. Для цехов постройки 60-х гг. прошлого столетия получить данные о работе оборудования оказывается вдвойне сложной задачей.
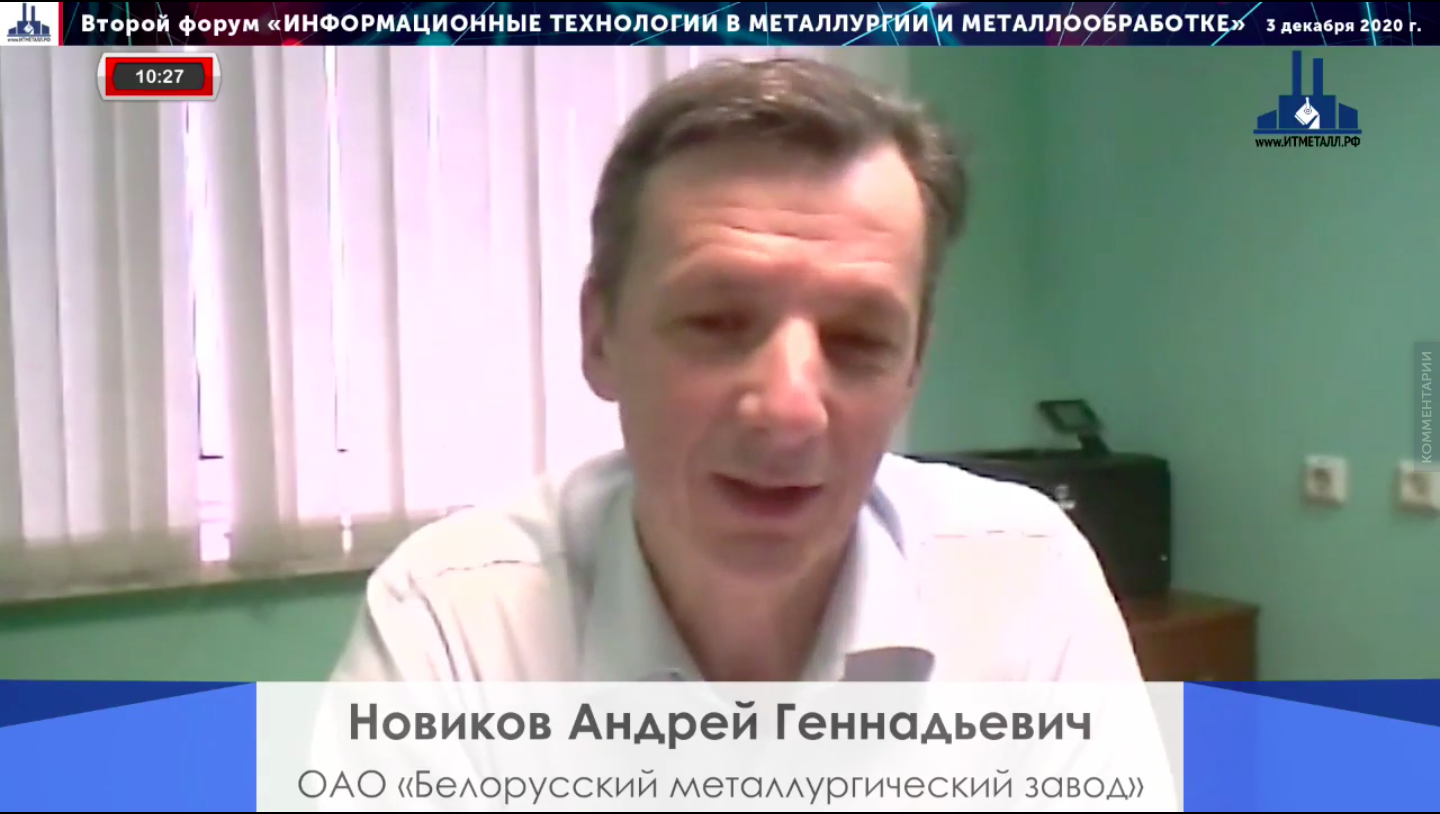
У белорусских металлургов этап активного использования искусственного интеллекта еще не начался. Андрей Новиков пояснил: «У нас никаких проектов запланировано не было – мы пока только присматриваемся к тенденциям и изучаем инструменты. Впрочем, с инструментами все понятно, не хватает практических примеров и возможностей для применения, которые были бы подтверждены финансовыми показателями. В условиях кризиса у руководства нет доверия к прорывным технологиям, а ведь их внедрение требует расходования ценных ресурсов». Андрей Новиков отметил еще одну проблему: к искусственному интеллекту плохо относятся и руководство компании, и специалисты на местах. Считается, что системы машинного зрения более медлительны, чем специализированные датчики.
Ренат Назыров затронул важную проблему современных технологий искусственного интеллекта для промышленного применения – отсутствие достаточного количества правильно размеченных данных и их качество. «Технологи собирали только те данные, которые им нужны для управления технологическим процессом, а другие не сохраняли. Им и в голову не могло прийти, что эти данные будут важны для обучения моделей искусственного интеллекта. Из-за этого возникают проблемы разрозненности данных и их чистоты, дублирования и противоречивости. Для их решения РУСАЛ планирует внедрить единую технологическую платформу, которая будет собирать максимальное количество данных вне зависимости от потребностей технологов». Аналогичным путем сейчас идут и некоторые нефтяные компании.
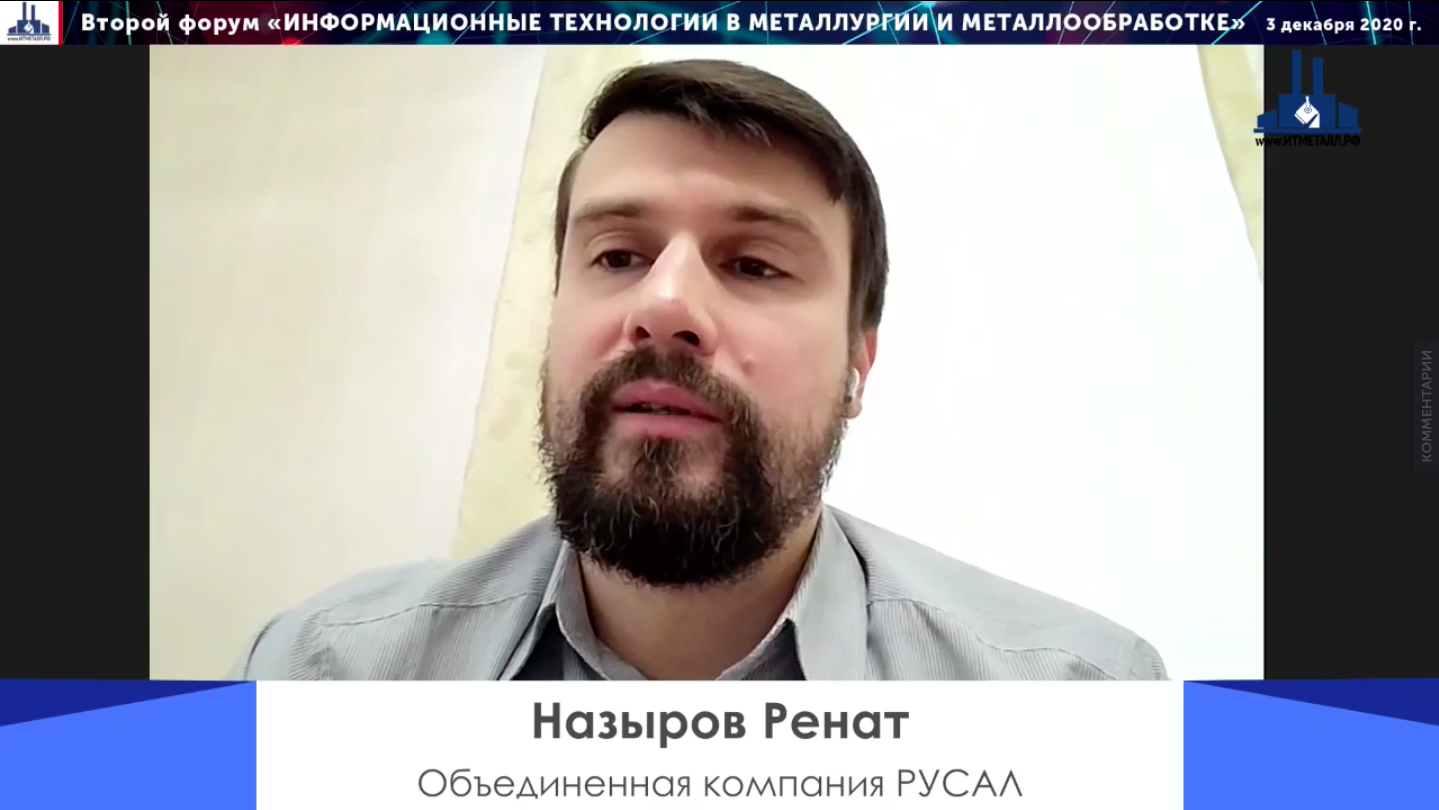
Для изучения бизнес-применения технологий искусственного интеллекта РУСАЛ запускает различные прототипы. Параллельно компания собирает все технологические данные для масштабного обучения моделей. «У нас есть проект в электролизе, поскольку для РУСАЛа это основа технологического производства, – рассказал Ренат Назыров. – Электролизеров в РУСАЛе тысячи, что позволяет собрать много данных. Однако нужно понять, чем данные одного электролизера отличаются от других аналогичных устройств. Мы используем видеоаналитику для анализа дополнительных выбросов в электролизерах, что является нарушением технологического процесса. Причем видеоаналитика оказалась дешевле, чем дооснащение электролизеров специальными датчиками. Видеоаналитика позволяет с помощью нескольких камер и сервера оперативно выявлять критические ситуации, а иногда даже предсказывать их и вовремя принимать меры, чтобы снизить выбросы и улучшить технологию». В компании также развивается проект по предупреждению о выходе из строя печей спекания, для чего используются термосканы (приборы для фиксации температуры в печи) и данные из АСУ ТП по технологическому процессу. Предполагается, что на основе этих данных можно прогнозировать возникновение критических ситуаций в поведении печи.
Цифровая помощь
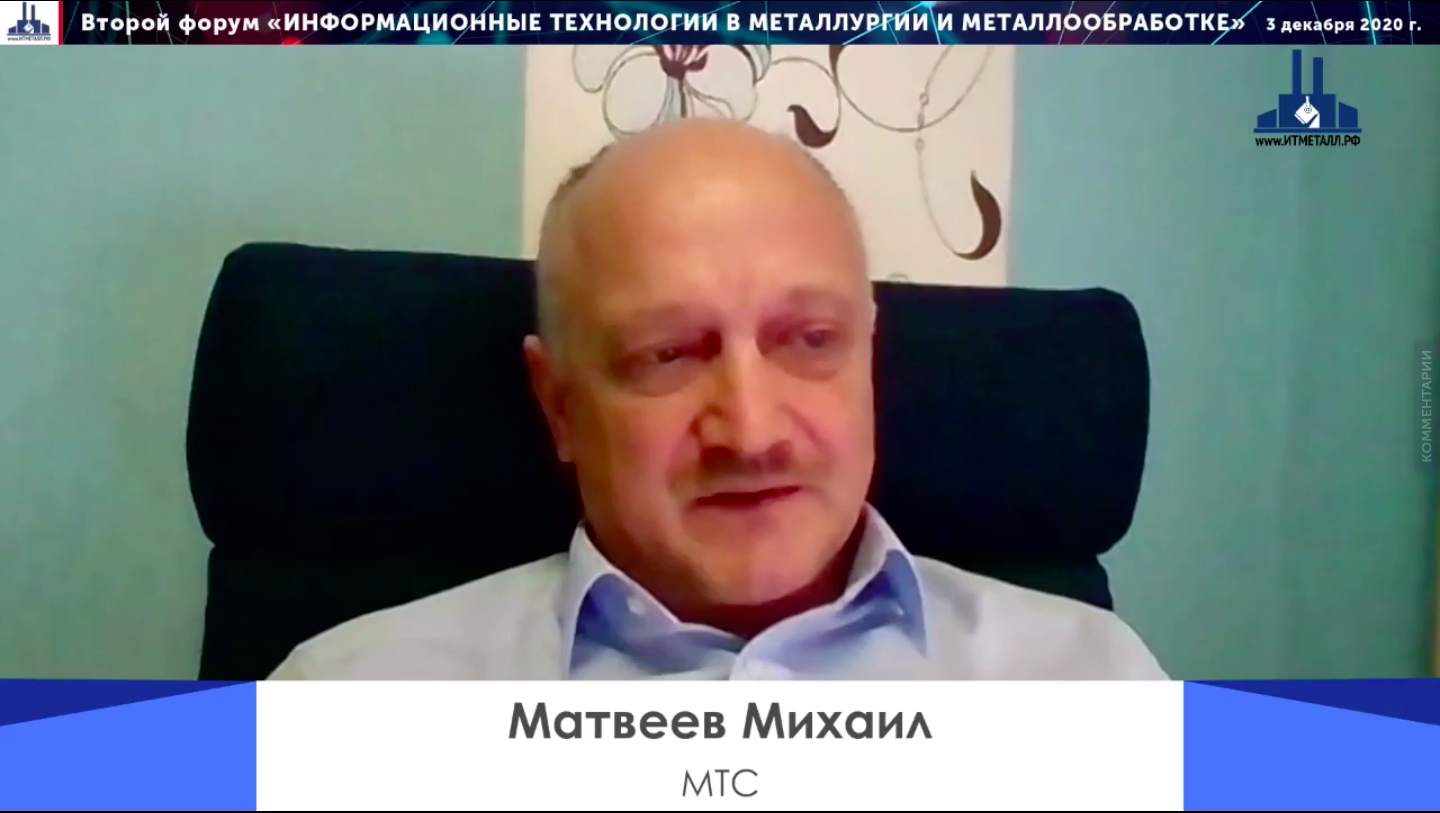
Важной темой цифровой трансформации являются компетенции персонала и возможность использования современных методов работы. Для этого разрабатывается целый класс решений, которые называются цифровыми помощниками. Эту тему на панельной дискуссии поднял Михаил Матвеев. По его словам, пятое поколение мобильной связи возникло во многом из требований цифровой промышленности. «Мы развиваем цифровых помощников для промышленных решений и уже реализовали несколько проектов с использованием цифровых помощников для выявления дефектов или улучшения технологического процесса. Однако для их внедрения необходимы базовые технологии промышленной цифровизации – это и датчики, и IoT, и сбор данных, и машинное обучение, и искусственный интеллект, который позволяет предсказывать определенные события». Компания МТС разработала для «Уралхима» цифрового помощника, который помогает правильно изготовлять азотно-фосфорные удобрений. Аналогичная технология может быть применена и в металлургии, где много усилий тратится на создание новых типов высокопрочной стали.
В целом же в рамках Индустрии 4.0 рекомендуется активно собирать данные для обучения механизмов искусственного интеллекта и построения новых моделей производственных процессов. Уже разрабатываются решения, которые с помощью компьютерного стереоскопического зрения с использованием технологии лазерной подсветки позволяют выявлять дефекты на прокате со стопроцентной точностью при очень высокой скорости выдачи готовой продукции. Без машинного зрения технолог, который следит за качеством проката, может и пропустить некоторые дефекты. МТС предлагает производственным компаниям совместные разработки с Huawei и «Сколково» для организации мобильных «краевых» вычислений (MEC), которые обеспечивают возможность работать и в производственных помещениях в режиме реального времени.
Леонид Аникин также отметил, что в последние несколько лет много технологий перешло из индивидуального применения в корпоративное и цифровые помощники – одна из них. Единое окно, синхронизация всех сервисов в одном API – основной тренд текущего года. Появились единые приложения для сервисов, а в приложения, например, для доставки еды, начинают встраивать функции по вызову такси. Следующий шаг – интеллектуальные колонки, которые понимают человеческую речь. Фактически они становятся новым интерфейсом для получения доступа к большому списку интеллектуальных сервисов. Аналогичная задача существует и на корпоративном рынке. Чтобы персонал мог эффективно общаться во время работы в заводских помещениях с большим количеством корпоративных приложений, необходимо создать специальное приложение, которое позволит получать наиболее важные сведения с помощью голосового интерфейса. Система должна постоянно дообучаться и отслеживать сложные области знаний. Законченных проектов в России не много – в 2020 г. было реализовано всего около десятка.
«У нас был интересный проект с НЛМК, где с помощью цифрового помощника была построена система по взаимодействию с их поставщиками, – привел пример Леонид Аникин. – Цифровому помощнику доверили выяснение того, чего именно хочет поставщик, обращаясь в отдел закупок компании. Это однотипные вопросы, и их автоматизация позволила сократить коммуникацию с отделом закупок». Впрочем, для Mail.ru самым крупным проектом по формированию цифрового помощника является интеграция корпоративных сервисов внутри Mail.ru.
Александр Лунев считает, что понятие «цифровые помощники» чуть шире, чем машинное зрение и искусственный интеллект. На производстве особенно важно применять специализированные ИТ-решения, которые позволят персоналу совершать меньше ошибок или чуть быстрее принимать решения. Причем в них не обязательно должны использоваться технологии искусственного интеллекта или машинного обучения. Даже с помощью простого сценария, который будет в нужное время подсказывать персоналу его дальнейшие действия, можно добиться многого.
Цифровые вещи и двойники
В последнее время много говорят о промышленных интернет-вещах (IIoT), которые должны прийти на смену простым датчикам АСУ ТП, однако далеко не все понимают, чем они отличаются. В современном цифровом понимании IIoT – это беспроводные датчики, которые общаются между собой или при необходимости с центральной станцией. «В РУСАЛе сейчас тестируются беспроводные датчики вибродиагностики, которые могут быть установлены на различных агрегатах в целях сбора с большой дискретностью данных по вибрациям, температуре и другим параметрам, которые позволяют оценить качество работы агрегата, – продолжил Александр Лунев. – При этом нет необходимости в подводке питания и прокладке дополнительных линий связи – используется технология LoRa WAN. Такие датчики устанавливаются на агрегат и работают в течение года, не требуя подзарядки. Проблема применения технологии LoRa WAN на металлургическом производстве – экранирование ее сигналов железобетонными конструкциями и агрегатами, что требует установки дополнительных базовых станций. Сейчас мы проверяем возможности этой технологии и требования по покрытию территорий завода сетью дополнительных базовых станций».
Использование подобных технологий открывает большие возможности по работе с данными, не требуя дополнительных вложений в сетевую инфраструктуру, – достаточно установить базовую станцию и необходимый набор модулей. Современная парадигма сбора данных в промышленности заключается в том, что приборы могут самостоятельно общаться между собой, оперативно принимая решения в соответствии с заранее установленными правилами. Классические датчики АСУ ТП на такое не способны: у них все взаимодействие идет через АСУ ТП, которое и принимает решения. Сейчас используются распределенные системы управления, которые позволяют получать информацию от различных датчиков, коррелировать ее между собой и на основе полученных данных оптимизировать технологический процесс в зависимости от происходящих в оборудовании процессов или загруженного сырья. Современные промышленные технологии настолько сложны, что взаимовлияние различных переделов не всегда могут оценить даже технологи с большим опытом работы, поскольку они не видят общей картины.
Андрей Новиков подтверждает, что в металлургии беспроводные датчики и видеоаналитика, которая используется для расширения поля сбора данных, – это основное направление развития. Они не требуют больших затрат на инфраструктуру и модернизацию существующих производственных сетей. Возможности этих технологий изучают все металлургические предприятия. Его компания также экспериментирует с LoRa WAN, пока же оснащает беспроводными датчиками вибрации и температуры прокатное производство.
Изучением возможностей вибрационных датчиков для предиктивной аналитики и обслуживания по фактическому состоянию оборудования занимается и ЧТПЗ. Видеоаналитика в горячих цехах работает не очень хорошо, поскольку на видео появляется достаточно много отражений – металлической пыли, дымов, конструкций и агрегатов, которые затрудняют работу систем распознавания. Возникают и проблемы с доставкой видеосигнала по радио, поскольку требуется достаточно высокая пропускная способность. Широкополосные технологии радиосвязи в цехах также неэффективны, поскольку слишком много помех и железных конструкций. В то же время LoRa WAN – технология передачи небольших объемов данных, что и позволяет довольно эффективно использовать ее на производстве.
Основная цель сбора данных в производстве – максимально точно представить текущее состояние технологического процесса, т. е. построить его цифровой двойник. Правда, по мнению Евгения Зайцева, для небольших предприятий применение цифровых двойников кажется не очень оправданным: «Зачем нам моделировать то, что видно всем с любой точки?» Однако оказалось, что механизмы моделирования, которые заложены в концепции цифрового двойника, можно использовать на защите производственной программы, где анализируются разные предложения по развитию производственной линии и увеличению ее производительности. «Генеральный директор спросил нас: «А вы можете доказать, что реализация этого проекта позволит повысить производительность на 0,2 трубы в час по всей линии? Только в этом случае потраченные деньги окупятся, – рассказывает Евгений Зайцев. – Мы приняли этот вызов и проанализировали несколько вариантов того, как доказать эффективность реализации конкретного проекта. Использовали различные среды моделирования – и 3D, и игровые движки, но остановились на одном западном продукте, который позволяет полностью промоделировать весь производственный цикл с помощью математических моделей. Прорисовали в этом инструменте один из цехов и поняли, что ошибались в оценке влияния маленького участка на весь производственный процесс. Теперь мы знаем, что при помощи цифрового двойника мы можем уберечь компанию от излишних инвестиций».
Сейчас ЗТЗ совместно со «Сколково» и компанией Cyberphysics прорабатывает физико-математическую модель участка покрытия трубы полиэтиленом, где нужно оценить необходимое количество полимерных материалов в зависимости от скорости движения трубы, марки полиэтилена и его вязкости. Такая модель позволит получить конкретные результаты вследствие сокращения затрат на сырье. Подобные точечные цифровые двойники для предприятий металлургии наиболее интересны и не очень затратны. В то же время цифровой двойник всего производства позволяет не только решать небольшие тактические задачи по оптимизации конкретных технологических процессов, но и правильно понимать, какие вещи в транспортной системе производства надо улучшить, чтобы ускорить производство продукции. В некоторых случаях, по словам Евгения Зайцева, удается показать руководству, что, например, перемещение труб краном дает возможность увеличить производительность конкретного участка на полтрубы в час.
Александр Лунев подтвердил, что в первую очередь нужно исходить из задачи и считать экономику внедрения цифрового двойника. «Мы занимаемся разными направлениями, – пояснил он. – Используем и конечно-элементные модели для решения технологических задач, и логистические модели, и модели оптимизации с применением технологий машинного обучения. В целом решаем локальные задачи, но в случае необходимости можем объединить модели для получения и оптимизации общей картины. Собрать все задачи вместе и получить полный цифровой двойник производства мы еще не готовы. На это нужно потратить слишком много ресурсов, а эффект пока не совсем понятен».
Эффективность частичных цифровых двойников подтверждает и Андрей Новиков: «Каждое предприятие имеет какой-то элемент цифрового двойника и уже использует математические и физические модели своих агрегатов и производства в целом. Направление перспективное, и мы, как и все, этим тоже занимаемся». По его словам, в Беларуси наиболее активно используют методологию цифровых двойников предприятия машиностроения. Там она имеет расширенный набор применения, поскольку для машиностроения цифровой двойник продукции и есть конечная цель, к которой они стремятся. Для металлургии четкого понимания этой тенденции не прослеживается. Даже если предприятие построит расширенную цифровую модель чего-то, то с окупаемостью пока больше вопросов, чем ответов.
В РУСАЛе, по словам Рената Назырова, используют цифровые двойники глиноземного производства. Цель этих моделей – описать финансовые, технологические и химические процессы, чтобы можно было работать с изменением качества сырья и технологии не на реальном объекте, а на цифровом двойнике и анализировать то, что будет происходить при изменении параметров. Этот проект реализован много лет назад, используется на всех глиноземных предприятиях РУСАЛа и хорошо оценен технологами и производственниками. Люди уже не мыслят старыми стереотипами «попробовали и получили», а могут прогнозировать результат с заранее заданными параметрами. В настоящее время РУСАЛ заканчивает строительство нового завода алюминиевого дивизиона и планирует сделать его полностью цифровым. Был сформирован пакет технических заданий по комплексной цифровизации предприятия, и одним из его пунктов являются цифровые двойники, которые и станут основой цифровизации. «Преимущества можно получить от цифровых двойников только при построении комплексной системы, а не при внедрении отдельных решений», – считает Ренат Назыров.
Направления цифровизации
По окончании панельной дискуссии прошли тематические сессии. С презентациями выступили 22 специалиста, представляющие компании ООО «ЕвразХолдинг», АО «АК Алтыналмас», ПАО «ТМК», ERG (Евразийская Ресурсная Группа), ООО «Мечел-Сервис», ООО «ММК-Информсервис», АО «АрселорМиттал Темиртау», ПАО «Северсталь» и др. Своим мнением о цифровизации предприятий металлургической отрасли поделились представители практически всех крупных холдингов. Цель большинства выступлений – обмен практическим опытом и обсуждение достигнутых результатов. Доклады экспертов были сгруппированы в три сессии: «Ключевые направления цифровизации», «Корпоративное управление», «Производство, логистика и сбыт». В рамках первого заседания обсуждались общие вопросы построения информационной инфраструктуры промышленных предприятий.
В частности, Леонид Аникин в своем докладе «Цифровизация. Как определить приоритетные проекты» рассказал о концепции цифровой трансформации промышленных предприятий, причем не только внешнего представления в виде цифровых сервисов, но и внутренней инфраструктуры. Кроме того, представил конкретные цифровые сервисы для промышленных предприятий во всех четырех областях цифровой трансформации: ИТ-решения, производственные процессы, корпоративные коммуникации и взаимодействие с клиентами. Компания разработала достаточно широкий набор решений, которые могут быть развернуты как во внутреннем облаке компании, так и на платформе самого Mail.ru.
Доклад директора по развитию ООО «ЕвразХолдинг» Максима Феопентова был посвящен продвинутой аналитике, которая стала частью стратегии цифровой трансформации компании «Евраз». Предполагается, что она позволит на базе собираемого массива данных, обработанного с помощью статистических моделей и искусственного интеллекта, обеспечить поддержку обоснованного принятия управленческих решений. Речь идет об оптимизации производственного процесса и стабилизации качества выпускаемой продукции на должном уровне. На предприятии планируется развернуть такие инструменты, как информационные панели с ключевыми показателями эффективности, система цифровых помощников с элементами искусственного интеллекта и построение цифровых двойников технологического процесса. Программа запущена в 2020 г., а в 2021 г. будут реализованы проекты с наибольшим экономическим потенциалом.

Построение «Цифрового рудника» описала в своем докладе Жанара Аманжолова, вице-президент по ИТ и корпоративному развитию казахской золотодобывающей компании АО «АК Алтыналмас». Проект стартовал в 2017 г. До недавнего времени компания занималась строительством базовой ИТ-инфраструктуры, низкоуровневой автоматизацией и разработкой методологической базы для развития бизнеса. В 2020 г. была разработана стратегия развития до 2024 г., в которой и предусмотрена цифровая трансформация предприятия. Подробно Жанара Аманжолова рассказала о пилотном проекте по предиктивной аналитике замены мельничных шаров в основной мельнице предприятия, что позволит компании, по предварительным оценкам, ежегодно экономить до 865 тыс. долл.
О проекте создания цифрового двойника для нового поколения непрерывных станов для производства труб рассказал в своем выступлении руководитель лаборатории цифровых технологий ООО «ТМК НТЦ» Евгений Шкуратов. На предприятии создан программный комплекс, который позволяет с помощью математических моделей управлять прокатными станами с высокой степенью автоматизации, которые были построены в 2008 г. на АО ТАГМЕТ и в 2014 г. на АО СТЗ. Система дает возможность оптимизировать скорость производства труб, их качество, расход материала и срок работы оборудования. При моделировании используются как математическое, так и нейросетевое моделирование технологического процесса. Цифровой двойник выдает рекомендации по стабилизации технологического процесса непрерывного производства труб, что обеспечивает их качество и объем выпускаемой продукции.
Офисная рутина
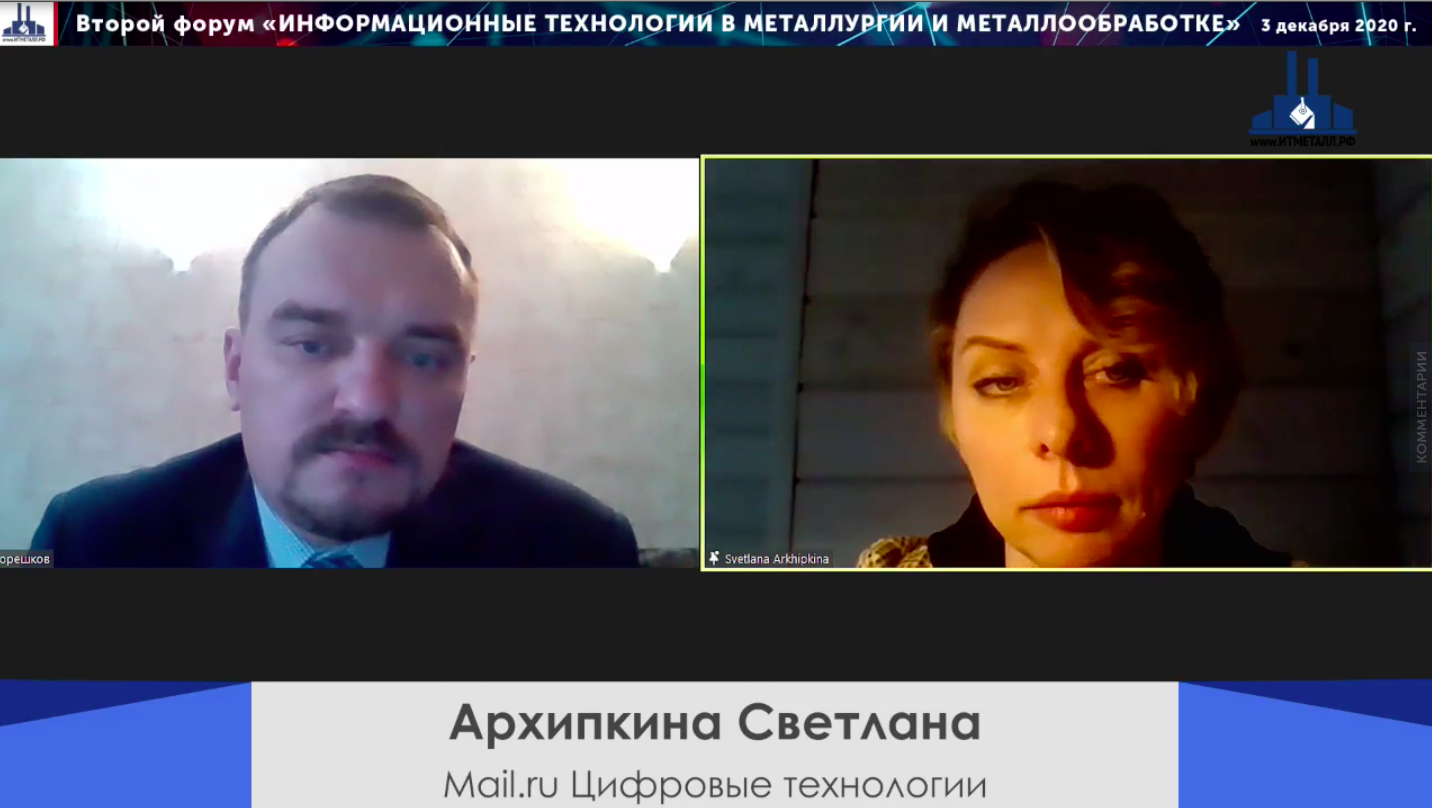
Вторая сессия была посвящена автоматизации рутинных операций с помощью RPA и цифровых ассистентов, а также электронному взаимодействию как внутри компаний, так и с контрагентами. В частности, тему раскрыла Светлана Архипкина, директор по развитию AI проектов «Mail.ru Цифровые технологии», которая рассказала о концепции цифрового помощника – и для взаимодействия с внешними контрагентами, и для внутренних коммуникаций с информационными системами предприятия. Mail.ru разработала платформу для построения чат-ботов, которые позволяют сотрудникам взаимодействовать с корпоративными системами предприятия на естественном языке. Для этого используется технология искусственного интеллекта по работе с естественным языком. Цифровые ассистенты позволяют сотрудникам и внешним контрагентам взаимодействовать с информационными системами предприятия не напрямую, а посредством естественного языка вопросов и ответов, как в текстовом виде, так и с помощью голоса. Сейчас Mail.ru занимается разворачиванием подобных решений на промышленных предприятиях по всей России.
Об автоматизации процесса поиска закупочных цен на сырье рассказал в своем выступлении руководитель управления промышленного искусственного интеллекта компании ERG Евгений Кравченко. Система собирает данные по ценам на сырье из различных источников: агрегатора цен Seldon, центра мониторинга, государственных закупок и прайс-листов самих производителей, затем производит очистку и стандартизацию данных, выполняет поиск оптимальной цены в зависимости от потребностей компании и выдает рекомендации для закупки. Система позволяет оптимизировать работу отдела закупок и обеспечить поставку в срок необходимого сырья по оптимальной цене и необходимого качества.
Про оборотную сторону медали – автоматизацию коммерческого блока – рассказал на конференции руководитель проекта внедрения CRM-системы в ПАО «ТМК». Его доклад был посвящен использованию роботов в дирекции по маркетингу ТМК, внедрению CRM-системы для автоматизации взаимодействия с клиентами и автоматизации разбора тендерной документации посредством нейронной сети. В маркетинговом отделе, как и у закупщиков, собирают множество информации о ценах из открытых источников, но анализируют ее для определения конъюнктуры рынка и проведения правильной ценовой политики. Технология CRM не является новой, тем не менее она позволяет работать с клиентами по различным каналам взаимодействия, анализировать воронку продаж и оптимизировать для клиентов взаимодействие с коммерческими службами ТМК. Анализ тендерной документации для поиска предложений на поставку также можно доверить технологиям искусственного интеллекта, поскольку до формирования интересных предложений необходимо обработать огромное количество запросов на покупку, нормализовать условия поставок и выбрать наиболее подходящие контракты.
В этой же сессии было два доклада, посвященных автоматизации документооборота в металлургической отрасли. Директор департамента ИТ ООО «Мечел-Сервис» Роман Тупкало рассказал о выборе ЭДО для юридически значимого взаимодействия с внешними контрагентами, поставщиками и заказчиками, а руководитель проекта АТАЧ ООО «ММК-Информсервис» Дина Бахарева – о разработке собственный системы электронного документооборота для сотрудников компании. И если в первом проекте необходимо было придерживаться стандартов электронного взаимодействия, то во втором важнее было обеспечить удобство работы с электронными документами, поддержку различных устройств, в том числе мобильных, а также экономию времени на работу с «электронной бюрократией».
Еще одним примером организации электронного взаимодействия с внешними контрагентами стал проект ЗТЗ по внедрению системы АСУ транспортной логистики (АСУ ТЛ), о котором рассказал на форуме Евгений Зайцев. Система предназначена для управления парком железнодорожных вагонов и взаимоотношениями с РАО РЖД. Решение интегрируется с принадлежащей РЖД автоматизированной системой ЭТРАН, а также с внутренними SAP ERP, «1С:MES» и электронного документооборота. Внедрение системы позволило повысить точность планирования поставок компании, проводить мониторинг логистических процессов и оперативно реагировать на изменения, вызванные внешними факторами.
Следующие два доклада были посвящены автоматизации рутинных операций с документами при помощи RPA. Так, ведущий специалист Центра компетенций RPA и инноваций ООО «ММК-Информсервис» Сергей Красильников рассказал о стремительном распространении технологии RPA на предприятиях группы ММК. Эта деятельность была начата в 2018 г., и на текущий момент в компании на постоянной основе действует более сотни программных роботов. ММК планирует для каждого сотрудника разработать робота-помощника, который будет выполнять за него все необходимые рутинные операции. А руководитель проекта RPA и чат-ботов компании АО «АрселорМиттал Темиртау» Татьяна Полиняк рассказала о внедрении на их предприятии не только RPA для автоматизации рутинных операций, но и чат- и telegram-ботов, которые оптимизируют горизонтальное взаимодействие в их компании. Основная задача этих инструментов – сократить время сотрудников на выполнение их штатных обязанностей.
Важной частью цифровизации промышленности является обеспечение безопасности технологического процесса. Руководитель направления собственных продуктов АМТ-ГРУП Вячеслав Половинко рассказал о необходимости выделения промышленного сегмента сети и обеспечения для него повышенных требований к безопасности, в целях чего используются решения типа Cross Domain Solutions (CDS). Одним из них является разработанный компанией АМТ-ГРУП InfoDiode, который предназначен для однонаправленной передачи данных, в частности в промышленных сетях. Решения этого класса позволяют более строго соблюдать требования информационной безопасности, причем как на логическом, так и на физическом уровне. Даже если хакеры и взломают данное устройство, они не смогут передать по нему информацию в другую сторону, поскольку в конструкции физически нет оптических излучателей для этого.
Начальник управления средств защиты ИТ-инфраструктуры ПАО «ТМК» Антон Кокин раскрыл подробности выбора решения для построения центра реагирования на компьютерные инциденты (SOC). Он отметил, что цифровая трансформация приводит к тому, что критические бизнес-процессы на предприятии становятся зависимы от ИТ, которым необходимо обеспечить эффективную защиту. Кроме того, все больше облачных решений внедряется на предприятии и приходится осуществлять передачу большего количества данных во внешнюю неконтролируемую среду. Это приводит к размытию периметра и усложнению составления правил информационной безопасности. Для обеспечения защиты своих цифровых активов компания решила привлечь коммерческий центр мониторинга – коммерческий облачный Solar JSOC компании «Ростелеком-Солар», который обрабатывает сообщения от установленных на предприятиях ТМК систем обработки событий безопасности SIEM. В 2019 г. начался процесс подключения предприятий к этому центру мониторинга.
Промавтоматизация
Предметом обсуждения на заседании третьей сессии стали прикладные аспекты автоматизации: частные облака, беспилотные летательные аппараты, 5G и IoT, обеспечение информационной безопасности и оптимизация производства с помощью инструментов искусственного интеллекта. В частности, Мария Грачева, руководитель группы промышленности «Mail.ru Cloud Solutions» рассказала об использовании облачных технологий, разработанных компанией. Mail.ru, накопив достаточно опыта в построении облачных решений в собственных ЦОД, теперь предлагает поделиться им с промышленными предприятиями. Компания выпустила на рынок продукт для построения частного облака на технологиях Mail.ru. Она может установить у себя внутри часть облака Mail.ru и запустить в нем сервисы компании как внутренние. Причем в случае необходимости можно будет часть из них перенести и в основное облако.
Директор по развитию компании Skymec Сергей Заверткин рассказал, как с помощью беспилотных летательных аппаратов можно оцифровать поверхность Земли. Технология позволяет даже оценить запасы руды и других материалов, сваленных в кучи на территории складов промышленных предприятий. Специальный дрон строит трехмерную модель местности с грудами материалов, а потом по цифровой модели можно оценить объем складированных материалов и вычислить их примерное количество. Подобная технология может пригодиться горнодобывающим компаниям и металлургам для быстрой оценки запасов промышленных материалов.
Перспективы использования технологии 5G на предприятиях описала в своем аналитическом докладе Наталья Пчеловодова, партнер J’son & Partners Consulting, отметив большие перспективы 5G для промышленности, поскольку сама технология была разработана с учетом требований промышленных предприятий. Она позволяет добиться низких задержек и передачи большого объема данных. Наиболее эффективное применение технология могут найти на транспорте и в логистике, в строительстве и машиностроении. В металлургической промышленности также есть задачи и по логистике, и по строительству, и по управлению парком автомобилей, что позволяет использовать в этих сегментах технологии 5G с низкой задержкой.
Михаил Матвеев, директор центра промышленной автоматизации компании МТС привел примеры таких компаний, как «Микрон», «Уралхим», Кировский завод, где были внедрены IIoT-решения для сбора данных с технологического оборудования. В частности, на предприятиях «Микрона» была создана система предсказания дефектов в выпускаемой продукции. Причем в 92% случаев для повышения качества продукции достаточно было вовремя заменить реактив, и система научилась это делать. На заводе «Уралхим» была разработана система, которая оптимизировала производственный процесс в нескольких цехах, стабилизировав технологический процесс, протекающий в котлах. Для Кировского завода компания МТС разработала систему обнаружения дефектов в металлопрокате, позволяющую выявлять брак в режиме реального времени. Сейчас технология вводится в опытную эксплуатацию.
Заключительные четыре доклада в этой сессии были связаны с проектами по использованию технологий искусственного интеллекта в промышленном производстве. Ведущий эксперт по автоматизации и цифровым технологиям ПАО «Северсталь» Андрей Федотов рассказал о применении методов глубокого машинного обучения для управления агрегатом непрерывного травления металла. Ведущий инженер ПАО «Челябинский трубопрокатный завод» Александр Дунаев поделился результатами использования машинного зрения для выявления дефектов в готовой продукции. Оказалось, что для этого проекта сложно было набрать необходимое количество фотографий с дефектами, которые не должны были появляться на металле, и пришлось эти дефекты делать самим, чтобы подготовить необходимое количество фотографий.
Директор департамента новых технологий компании «РУСАЛ Инженерно-технологический центр» Алексей Жердев рассказал о применении машинного зрения в системах контроля герметизации электролизеров, о которой в панельной дискуссии упоминал Ренат Назыров. В процессе исследования проводилось сравнение методов использования газоанализаторного оборудования и визуального наблюдения. Первый вариант оказался достаточно дорогим, потому от него пришлось отказаться. Было принято решение использовать видеокамеры для выявления нарушения герметизации электролизеров, поскольку каждая камера могла одновременно контролировать до десяти электролизеров, а система машинного зрения позволяла с высокой степенью достоверности определять нарушение герметичности каждого из них.
Финальный доклад прочитал ведущий инженер ПАО ЧТПЗ Михаил Ильиных, который рассказал о совершенствовании продукта под названием «Помощник сталевара», о котором на панельной дискуссии говорил Александр Лунев. Собственно, этот продукт был представлен еще в прошлом году на Первой конференции «Информационные технологии в металлургии и металлообработке». За год продукт сильно прирос в функционале, и теперь он обеспечивает не только экономию ферроматериалов при выплавке стали, но и множество сопутствующих функций, таких как подготовка отчетности, контроль энергопотребления, оптимизация закупки лома и т. д. Продукт развивается, и его уже вполне можно назвать цифровым помощником, который ускоряет принятие решений при выплавке качественного металла.
Заключение
Слушатели могли оценить доклады с помощью системы интерактивного голосования. При подведении итогов мероприятия были названы четыре лучших докладчика: Леонид Аникин, директор по развитию бизнеса «Mail.ru Цифровые технологии», Максим Феопентов, директор по развитию ООО «ЕвразХолдинг», Евгений Шкуратов, руководитель лаборатории цифровых технологий ООО «ТМК НТЦ», Михаил Ильиных, ведущий инженер ПАО «Челябинский трубопрокатный завод».
В целом можно сказать, что цифровая трансформация предприятий металлургической промышленности идет, хотя и не стремительно, но постепенно и вдумчиво, без излишней траты сил и ресурсов. Тем не менее искусственный интеллект в виде машинного зрения, предиктивной аналитики, RPA, цифровых двойников и чат-ботов находит свое место в бизнес-процессах промышленных компаний. Его перспективность уже не вызывает сомнений: он позволяет улучшить качество продукции, ускорить выполнение рутинных операций и быстрее принимать более эффективные решения как на производстве, так и в бизнесе.
Однако искусственный интеллект очень требователен к качеству и количеству данных. Для их сбора приходится внедрять технологии промышленного Интернета вещей, который сейчас используют в основном беспроводные технологии – мобильной широкополосной связи 5G или низкоскоростной, но энергетически эффективной LoRa WAN. Поэтому технологии LoRaWAN и 5G также начинают испытывать в тяжелых промышленных условиях, но о результатах говорить пока рано. Для оперативного получения данных о работе оборудования могут быть использованы и видеоподключения, которые хорошо взаимодействуют с системами искусственного интеллекта, – для них нужны широкополосные подключения.
В компаниях активно развиваются внутренние и внешние коммуникации: этот год стимулировал переход к электронным видам взаимодействия. И здесь на помощь также приходят технологии искусственного интеллекта, которые воплощаются в виде цифровых помощников, чат- или telegram-ботов, аналитических систем и многих других. Сейчас методы искусственного интеллекта применяются практически повсеместно, их пытаются внедрять во все используемые ИТ-инструменты. Металлурги тоже начинают использовать эти инструменты, а некоторые уже получили вполне хорошие результаты. Наша конференция как раз и задумывалась как площадка для обмена практическим опытом применения ИТ в металлургии, так что здесь уже можно найти первые положительные примеры промышленного применения искусственного интеллекта.